3 Minuten zu lesen
Automatisierung als Schlüssel zur effizienten Qualitätssicherung: Damit Kontrollen kein Risiko sind
Benjamin Brumm
:
Jul 22, 2025 7:45:00 AM
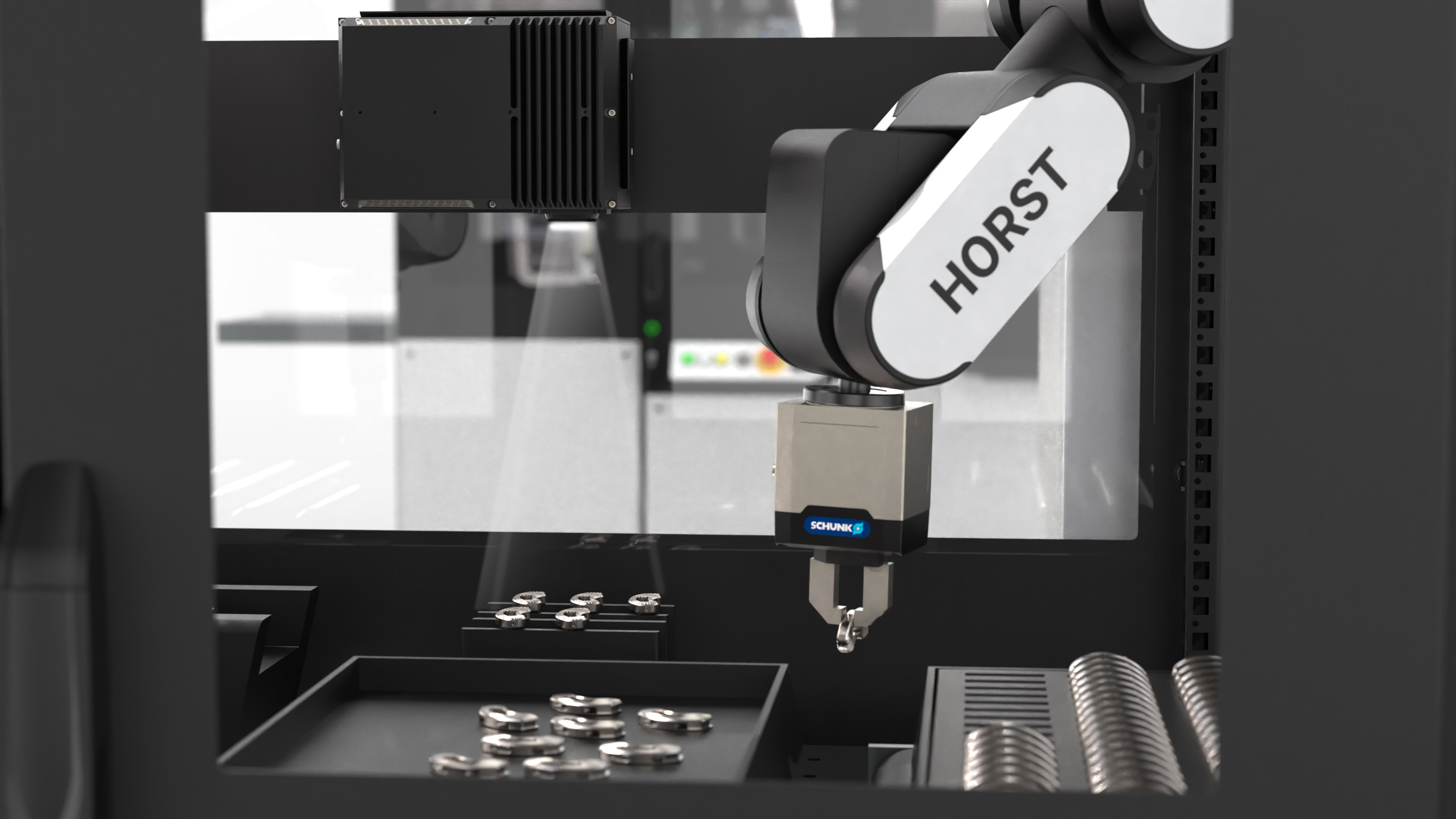
Im Werk eines bayerischen Herstellers von Titan-Implantaten für Wirbelsäulenchirurgie prägte lange eine einzige Zahl den Tagesablauf: 90.000 Teile pro Jahr, jedes sicherheitskritisch und zu 100 % zu prüfen. Die Qualitätssicherung übernahmen Fachkräfte von Hand: Lupe, Messschraube, Papierprotokoll. Geht hier Zeit verloren, wird die nachgelagerte Sterilisation blockiert. Am Ende von Verzögerungsketten in der Medizintechnik warten Patienten auf ihren OP-Termin.
Als in die Urlaubszeit eine unerwartete Krankheitswelle fällt, drohte dem Unternehmen eine Häufung nicht geprüfter Implantate. Der Produktionsleiter beschreibt diesen Wendepunkt so:
„Wir sahen zu, wie sich Paletten stapelten. Die CNC-Maschinen liefen perfekt, doch fünf Meter weiter lag unser Limit – ein Tisch mit Handlupen.“
Das Werk stand vor der Entscheidung: Weniger produzieren oder eine automatisierte Produktkontrolle, um auch weiter die hohe Qualität zu gewährleisten, für die das Unternehmen bekannt ist.
Kein Einzelfall: Drei von vier deutschen Medizintechnik-Herstellern sehen in den strikten Vorgaben, allen voran in der EU-MDR, und der damit zusammenhängenden Bürokratie laut einer Umfrage des Branchenverbands BVMed (Herbst 2024) ein großes Problem. Laut derselben Umfrage macht sich außerdem der Fachkräftemangel immer stärker bemerkbar, neben dem Vertrieb fehle es besonders in der Produktion an Mitarbeitern.
Aufbruch in die Automatisierung
Der Implantat-Hersteller entschied sich für die Automatisierung. Obwohl anfänglich Bedenken wegen der Komplexität und Kosten herrschten, sollte eine vollintegrierte Prüfzelle genutzt werden. Ziel: Die Bauteile ohne Wartezeiten aus der Fertigung in die Prüfung übernehmen. Vier Anforderungen hatte das Unternehmen bei der Marktrecherche:
- Kurze Inbetriebnahme – kompletter Ramp-up in unter vier Wochen, möglichst ohne hohen zusätzlichen finanziellen oder zeitlichen Aufwand für die Umsetzung.
- Validierung – Nachweis der Wiederholgenauigkeit und MDR-konforme Datenhaltung.
- No-Code-Software – die Automations-Software sollte weitgehend von den QS-Fachkräften selbst programmiert und bedient werden, zumindest für Anpassungen und die Prozesssteuerung sollten keine Experten benötigt werden.
- Standardisierte Bauweise – einfache Skalierung sowie Flexibilität für andere Implantat-Varianten.
Nach der Marktrecherche entschied sich das Unternehmen für eine individualisierbare Robotik-Lösung von fruitcore robotics auf Basis des 6-Achs-Roboters HORST600 mit einer Wiederholgenauigkeit von ± 0,05 mm und Multispektralkameras mit KI-gestützter Bildauswertung. Ausschlaggebend für die Entscheidung war die intuitive Automations-Software horstOS, die das QS-Personal innerhalb weniger Stunden einfach selbst bedienen konnte. horstOS umfasst neben der grafischen oder textuellen Programmierung auch die Einrichtung und Steuerung der Anlage.
Die neue Prüfstrecke im Praxistest
- Automatische Entnahme: Ein Roboter entlädt zunächst Implantate aus einer CNC-Maschine und platziert sie in ein Tray. Ein zweiter Roboter nimmt die Teile aus dem Tray heraus und rotiert sie vor der Spezialkamera.
- Inline-Prüfung: Mittels KI-Algorithmen der Line-Scan-Multispektralkamera ist es möglich, Kratzer ab 5 μm zu erkennen, die in der MDR vorgeschriebene Lasergravur zu prüfen und das Kantenprofil des Implantats zu vermessen – alles in 0,4 Sekunden.
-
Sortierung: Bauteile mit Abweichungen werden in ein Tray zur Nacharbeit gelegt, iO-Teile auf Transportträger für die Sterilisation. - Datendokumentation: Seriennummer, Bilder und Prüfurteil fließen über den Industriestandard OPC UA ins Manufacturing Execution System. Dieses schreibt alle Informationen automatisch in den elektronischen Device History Record, wie von der EU und der US-amerikanischen FDA verlangt.
- Nachweisbarkeit: Wünscht ein Kunde Fertigungs- und Prüfnachweise oder verlangt eine Aufsichtsbehörde danach, können diese mit einem Klick erzeugt werde, was das Fehlerrisiko und den Aufwand vor Audit-Prüfungen reduziert.
- Validierung und Wartung: Innerhalb von fünf Tagen konnte die neue Prüfanlage sowohl die vorgeschriebene Installation als auch die Operational Qualification durchlaufen, zwei Wochen dauerte die Performance Qualification. Um dauerhaft präzise Messergebnisse zu erhalten, erinnert ein integrierter Kalibrier-Assistent jährlich an die Re-Qualification, die remote durch einen Techniker von fruitcore robotics erfolgen kann.
Eine QS-Mitarbeiterin fasst zusammen:
„Früher prüfte ich 500 Implantate am Tag, heute überwache ich mehrere Tausend Datensätze und greife nur noch ein, wenn das Dashboard Besonderheiten zeigt. Der Job ist anspruchsvoller, aber deutlich weniger ermüdend."
Messbare Ergebnisse sechs Monate nach Start der Automatisierung
- Prüfzeit je Teil: von 60 auf 15 Sekunden (- 75 %)
- Durchlaufzeit pro Batch (300 Teile): 480 auf 90 Minuten (- 81 %) *
- Ausschussrate: von 1,2 auf 0,9 Prozent (- 25 %)
- RSI-Ausfalltage: von 12 auf 2 pro Jahr (- 83 %)
- ROI der gesamten Anlage: Amortisation in 19 Monaten
Warum ist die Prüfzeit pro Teil automatisiert so viel schneller?
Eine automatisierte Prüfzelle ersetzt sequenzielle Handarbeit durch einen einzigen parallelen Digitalvorgang. So schrumpft die Prüfzeit pro Implantat auf ein Viertel, während die Messqualität sogar steigt. Im Detail sind dafür folgende Hebel ursächlich:
- Eine Line-Scan-Multispektralkamera belichtet während einer einzigen 360-Grad-Rotation das komplette Implantat und sammelt dabei bis zu 40.000 Pixelzeilen pro Sekunde. Die Fachkraft müsste dieselbe Fläche mehrfach abfahren, am Mikroskop nachfokussieren und die Beleuchtung anpassen.
GPU-basierte KI-Algorithmen werten Kratzer, Lasermarkierung und Kantenmaß gleichzeitig aus. Manuell wären das drei getrennte Arbeitsschritte mit Lupe, 2-D-Code-Leser und Messschraube. Der Roboter legt das Teil exakt in die Messposition – kein Aufnehmen, Drehen, Ablegen; kein Wechsel zwischen Werkzeugen. Einen Großteil der ursprünglichen 60 Sekunden Prüfzeit fraßen genau diese Handbewegungen.
- Bilder, Seriennummer, iO/niO-Urteil landen direkt im System; bislang nötige Notizen, Stempel und Scans entfallen.
- Die Maschine liefert jeden Zyklus in exakt 15 Sekunden – ohne Mittagstief, Pausen oder Blickwechsel. Für Menschen ist diese Gleichmäßigkeit biologisch unmöglich.
Was den Ansatz von fruitcore robotics von anderen unterscheidet
Während klassische Automatisierungslösungen oft einzelne Bestandteile (z. B. Roboter, Kamera, Sicherheitstechnik, Software) bündeln, bietet fruitcore robotics alle notwendigen Bestandteile aus einer Hand an. Das reduziert den Aufwand und die Kosten der Integration, vereinfacht die Validierung und verkürzt Serviceeinsätze erheblich. Die offene Architektur der Software erlaubt außerdem, neue Prüfalgorithmen als Update einzuspielen: ein Vorteil, sollten die regulatorischen Anforderungen steigen oder sich ändern.
Blick nach vorn
Der bayerische Implantat-Produzent registriert seit der Einführung der Automatisierung den Abbau von Staus bei der Produktprüfung und eine lückenlose Datenerfassung. Kleinere Losgrößen, schnellere Produktwechsel und sofortige Audit-Bereitschaft sind heute dort Standard. Der Hersteller plant, ähnliche Robotik-Lösungen an zwei weiteren Standorten im Ausland zu installieren.
Fazit
Das Fallbeispiel zeigt, wie Automatisierung die Herausforderungen der Medtech-Qualitätskontrolle radikal minimiert. Der gesteigerte Durchsatz, die Normsicherheit und bessere Arbeitsbedingungen stellten sich nach der raschen Integration ein. Für die Branche, die von gleichzeitigem Wachstum bei regulatorischen Hürden geprägt ist, stellt sich die Automatisierung als pragmatischer Weg dar, um Effizienz, Compliance und Zukunftsfähigkeit zu vereinen.