2 min read
Multi-sensor system makes industrial robots even more precise and flexible
Benjamin Brumm
:
May 9, 2025 10:24:15 AM
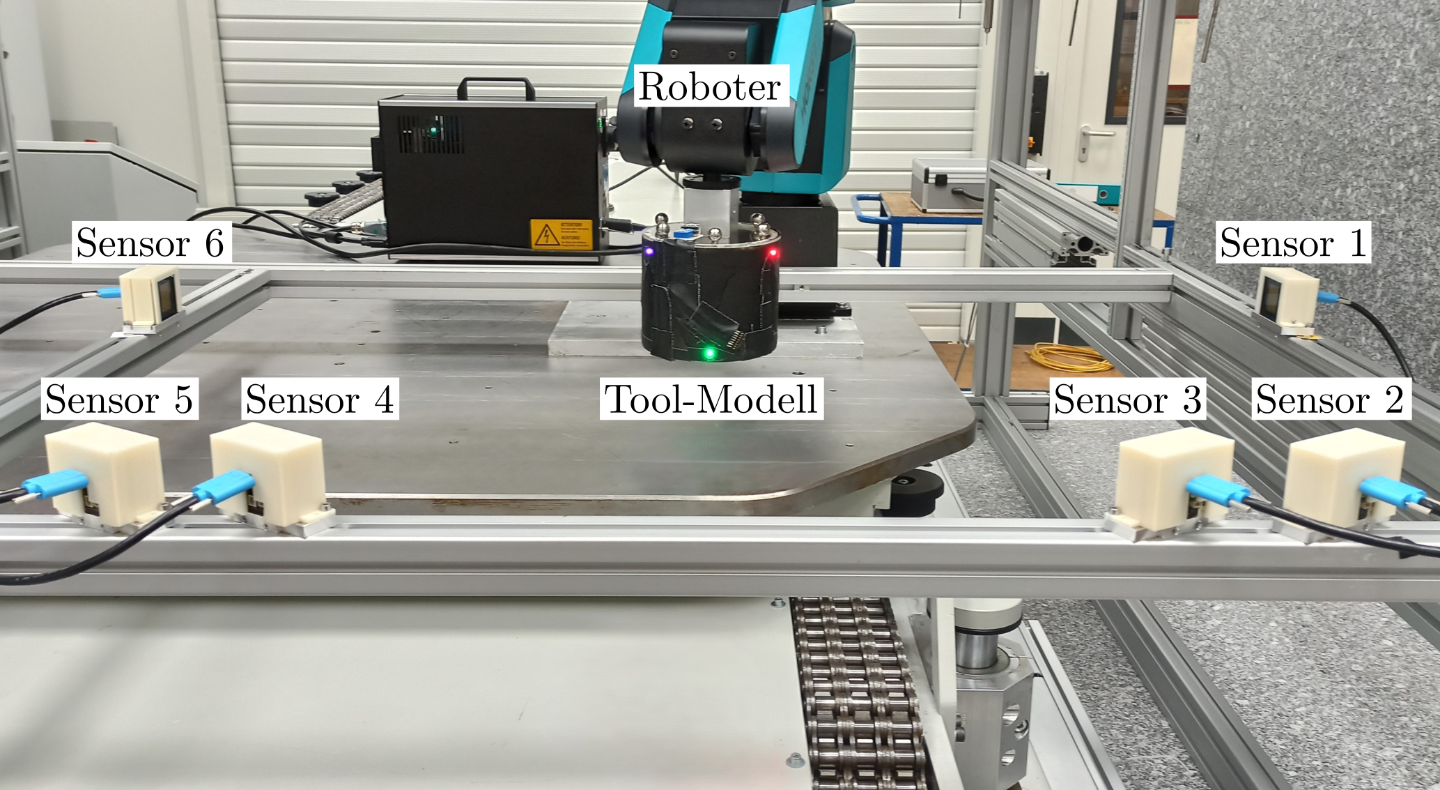
Industrial robots have established themselves in numerous manufacturing processes. However, precision and accuracy are particularly crucial in incremental forming technology: the high forming forces often lead to deviations that have so far severely limited the use of robots. Find out in this article how the Bremen Institute for Metrology, Automation and Quality Science (BIMAQ) and the Fraunhofer Institute for Machine Tools and Forming Technology (IWU) are developing a novel solution with a HORST600 robot system from fruitcore robotics that transforms standard industrial robots into true precision tools for production.
The challenge: precision versus flexibility
CNC gantry machines are precise but less flexible - industrial robots, on the other hand, impress with their adaptability, but so far at the expense of the required precision. Medium-sized companies in particular are looking for cost-effective and flexible technologies. Particularly in processes such as incremental sheet metal forming (IBU), in which complex sheet metal components are manufactured without cost-intensive forming tools, the use of robots has been difficult to date due to deviations under high loads.
IBU is used, for example, for prototypes, small series or individual parts, where the forming tool is moved step by step over the sheet metal until the desired geometry is achieved. To enable robots to achieve the necessary positioning accuracy, the researchers are developing a process called μRoboForm, for which they are using the fruitcore model HORST600, as it can easily meet the high requirements of the process.
The solution: an optical multi-sensor system based on the sundial principle
The central element of μRoboForm is the development of an optical multi-sensor system that measures the exact position and orientation of the tool center point (TCP) of the HORST600 robot in real time - with an impressive accuracy of less than 50 micrometers.
This high-precision measurement is possible thanks to LED markers on the tool and special shadow sensors, which provide reliable and interference-free data even under difficult conditions. The option of online data transmission to the controller enables immediate corrections to be made during the process in order to directly influence the precision and reliability of the robot.
Test with HORST600 from fruitcore
HORST600 from fruitcore robotics, a compact robot model that is particularly suitable for precision tasks thanks to its high repeat accuracy of ±0.05 mm and a payload of up to 3 kilograms , is being used as part of the research work. The use of HORST600 illustrates how flexible robots in combination with high-precision sensor technology can efficiently automate and optimize even demanding forming processes. This new possibility could permanently change manufacturing technology, especially for SMEs.
What does this mean for the industry?
- Greater precision: standard robots can be used for forming processes with tighter tolerances.
- Cost efficiency: Inexpensive robots such as HORST can be used instead of expensive special machines.
- New application possibilities: Industrial robots can now be used for even more demanding manufacturing tasks.
Conclusion: The next evolutionary step for industrial robots?
The precise real-time corrections provided by μRoboForm can make robots more interesting for companies that want to avoid the high costs of special machines but are dependent on extreme precision in the micrometer range. This makes it possible to dispense with expensive CNC gantry machines.
The joint project of the research institutes is funded by:
This article was produced with the kind support of the Fraunhofer Institute for Machine Tools and Forming Technology IWU.