Find your HORST: Simple, fast and a perfect fit with the product finder
Discover the ideal industrial robot for your specific needs. Transparent costs, customized software and service options. Just a few clicks will take you to your personal offer.
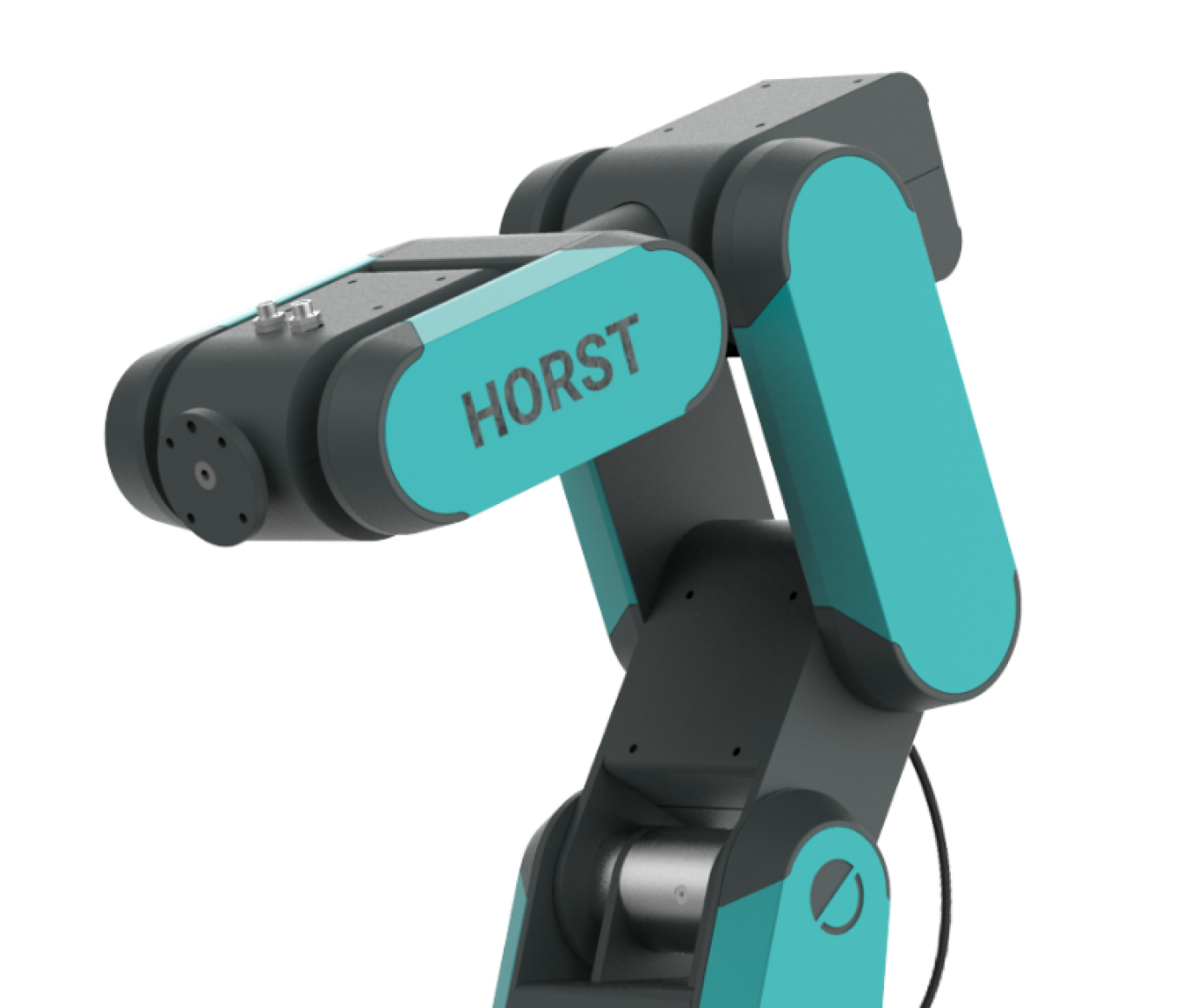
It's that easy to find the right Digital Robot for your applications
Forget the tedious and lengthy search for a suitable industrial robot for your company's challenges! With our product finder, you can put together the right all-inclusive automation package in just a few moments: transparent, requirements-oriented, user-friendly.1. Digital Robot
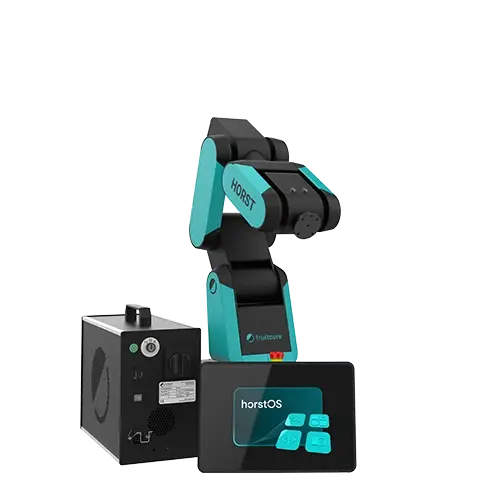
Range
The range refers to the workspace a robot can cover and is therefore crucial for its efficient use in manufacturing. Smaller ranges are ideal for assembly and pick-and-place tasks, while larger ones are suitable for applications such as welding or material handling. Very large ranges are used for handling heavy loads.
Maximum payload
The maximum payload of industrial robots refers to the maximum weight a robot can safely handle and move. It is a critical parameter to ensure the performance and safety of robots in industrial applications.
Application examples for maximum payloads
- Light payload (up to 10 kg): Pick-and-place robots in assembly lines, for example in electronics manufacturing.
- Medium payload (10-100 kg): Welding or painting robots in the automotive industry or machine manufacturing.
- Heavy payload (over 100 kg): Palletizing robots and lifting devices in warehousing and logistics applications, or robots handling heavy vehicle parts in the automotive industry.
Repeatability
The repeatability of industrial robots refers to the robot's ability to perform the same task precisely and reliably multiple times. High repeatability minimizes production errors and contributes to the optimization of processes. High-performance industrial robots are characterized by a repeatability of up to ±0.1 mm.
Maximum Speed (TCP)
The maximum speed (TCP) of industrial robots defines the time it takes to perform a task. A higher speed allows for processing more parts in a shorter time, increasing production throughput. High-performance industrial robots have a maximum speed of at least 3 m/s.
Advantages of higher maximum speeds:
- Increased productivity: A robot with a higher speed can process more parts within a given time frame, thereby increasing production output.
- Shorter cycle times: Faster movements can accelerate process workflows, leading to shorter cycle times and improved machine availability.
- More efficient resource utilization: A higher maximum speed allows for accomplishing the same work with fewer robots or maximizing the use of robots in a shorter time, resulting in more efficient investment and resource utilization.
- Faster return on investment (ROI): Since a higher speed leads to increased productivity, the investment in the robot can be recouped more quickly.
Axis
The number of axis in industrial robots indicates how many degrees of freedom they have, determining their flexibility and versatility in performing tasks. A higher number of axis allows for more complex movements and precise work in different spatial planes. In the industry, 6-axis robots are most common, as they offer particularly high flexibility and precision in their operation.
Weight
The weight of industrial robots affects their flexibility and applicability in manufacturing and production environments. A lower weight can facilitate the adaptation and integration of robots into existing systems, as well as accelerate the transition between different application areas.
Advantages of specific weight classes of robots
- 30 kg: Very lightweight and easy to transport, ideal for quick integration into assembly lines and applications with limited space.
- 60 kg: Offers a good balance between lightness and performance, enabling use in a wider range of applications and making transport and commissioning easier compared to heavier robots.
- 150 kg: This weight class allows for deployment in more demanding tasks that require higher payloads, while the robot remains lighter and easier to handle than very heavy industrial robots.
Ambient temperature
The ambient temperature is significant for industrial robots as it can affect their performance, reliability, and component lifespan. Ideally, industrial robots should operate in environments with moderate temperatures, typically between 5°C and 40°C (40°F and 100°F), to ensure optimal performance and longevity.
Sound level
The sound level of industrial robots indicates how loud the noises are that they produce during their operation. This value is measured in decibels (dB) and serves as an indicator of noise pollution in a production environment. Low sound levels in the range of under 70 dB correspond to a conversation at normal volume.
Protection class
The Ingress Protection (IP) rating of industrial robots indicates the extent to which they are protected against the intrusion of dust, solid objects, and water. The two digits in the IP classification represent the protection against solid objects (first digit) and water (second digit).
Power supply
The power supply of industrial robots is defined by the electrical power in watts (W), as well as the voltage (VAC) and frequency (Hz). Typical power supplies for industrial robots range from 200-600 VAC and 50-60 Hz, with larger robots requiring more power and thus having a higher energy consumption.
Digital inputs on tool flangeThe number of digital inputs for the tool flange of an industrial robot indicates how many digital signals can be received from a tool. These signals can include control commands that influence the operation of the tool. |
Digital outputs on tool flange
The number of digital outputs for the tool flange of an industrial robot indicates how many digital signals can be sent from a tool to the robot. These signals can be control commands for the robot or other components of the production process that should respond to the tool.
I/O power supply on tool flange
The power supply at the tool flange serves to operate tools, sensors, and actuators at the end of the robot arm. Typically, 24-volt voltage is used, while the current strength (amperage) varies depending on the requirements. Lower amperage values enable higher energy efficiency, reduced heat generation, lower cooling requirements, and cost savings through smaller cable cross-sections and lighter components.
Dimensions Control
The control cabinet of an industrial robot is designed to house the robot's control unit, containing all necessary electrical components and the programmable logic controller (PLC). More compact and space-saving solutions are useful, as they can be more easily integrated into existing production environments.
Digital inputs on switch cabinet
The number of digital inputs on the control cabinet of an industrial robot indicates how many signals from external sensors or devices can be received simultaneously. In industrial robotics, 16 to 32 digital inputs are common.
I/O power supply on switchThe power supply for the control of an industrial robot provides electrical energy to the control unit, motors, and sensors. Common voltage levels are 24 or 48 volts. Lower current values (single-digit amperage) have a positive impact on energy efficiency and cooling requirements, leading to cost savings. |
Safety-relevant Inputs (2 channels)Safety-relevant inputs with two channels on industrial robots ensure a high level of safety for the operation and protection of operators and equipment in accordance with DIN EN ISO 10218. The redundant arrangement reduces the risk of malfunctions, since both channels must match in order to recognize a signal as valid. The standard is intended to ensure that industrial robots function reliably and safely in critical situations in order to prevent accidents. |
Wiring between robot and controllerIndustrial robots are connected to their control units through multi-conductor cables that transmit both power supply and data and control signals. The length of the cable should provide enough slack for the robot's movements without causing tension or damage to the cable. |
Digital outputs on switch cabinet
The number of digital outputs on the control cabinet of an industrial robot indicates how many actuators and devices the robot can control. The digital outputs allow the robot to send signals to external devices such as valves, switches, or actuators to perform complex tasks. In industrial robotics, 18 outputs are a common number.
Safety-relevant output (2 channels)
Safety-relevant outputs with two channels on industrial robots are used in accordance with DIN EN ISO 10218 to ensure the safety of operators and equipment by sending redundant control signals to safety-critical components. The dual-channel architecture minimizes the risk of malfunctions, as both channels must match for a valid signal. When the standard is met, an industrial robot can operate reliably and safely even in critical situations.
Dimensions Panel
The dimensions of a control panel for industrial robots with graphical programming affect the user-friendliness and handling of the system. The overall size should provide a balanced combination of ergonomics and functionality.
Display specificationThe display for an industrial robot's operator panel should be high-resolution (for example, Full HD) and large enough to clearly and appealingly display details. A touchscreen is advantageous, as it allows for user-friendly operation, similar to that of a tablet or smartphone. |
Safety relevant emergency stopEmergency stop switches for industrial robots are mandatory to ensure safety in the workspace and minimize the risk of injuries. They work by immediately stopping the robot and interrupting the power supply to the motors when activated, resulting in an instant stop. |
Wiring between panel and controlThe control of industrial robots is connected to the operator panel via cable to transmit data and control signals. The length of the cable should be sufficient to allow comfortable operation of the panel and ensure the operator's freedom of movement. |
Safety relevant three-level enabling switch
Multi-stage enable switches for robot operation are mandatory because they provide an additional level of safety during manual control. They prevent unintentional movements or dangerous situations. If the enable switch is released while in manual mode, the robot's movement stops immediately.
Graphical programming on the panel
The graphical programming on the control panel provides a user-friendly interface for easily controlling robot movements and functions, even without extensive programming knowledge. This promotes efficient, adaptable control and directly improves productivity and efficiency at the facility.
Advantages of graphical programming on the panel:
- User-friendliness: An intuitive graphical user interface allows even individuals without programming knowledge to operate and adapt the robot. This promotes broader acceptance and usage of the robot.
- Efficiency improvement: Graphical programming enables tasks to be programmed and optimized more quickly and easily, leading to higher productivity and efficiency.
- Error minimization: The graphical user interface supports the detection and correction of programming errors, reducing the risk of errors that can lead to production downtime or damage to equipment.
- Cost savings: The simple programming and error correction save the company time and resources, resulting in a reduction of operational and maintenance costs.
- Flexibility: Graphical programming allows for quick adaptation and modification of robot functions to respond to changing production requirements. This increases the robot's flexibility and enables versatile usage in various application areas.
Access to licence management and Updates
Access to license management and updates allows for centralized management of robot software licenses and wireless updates. This keeps the robot control system up to date and ensures it continues to meet operational requirements in the future.
Advantages of this feature in practice
- The wireless installation of software updates and patches without manual intervention saves valuable work time and increases efficiency.
- Central management and monitoring of software licenses for all robots in the fleet reduces administrative effort and simplifies control over the entire robot inventory.
- Regular updates to the robot software can fix any defects and further improve the robot's performance after purchase, reducing the risk of production disruptions or failures.
- By accessing the latest features and improvements in the software, companies benefit from over-the-air technological advancements and the continuous development of the robots.
Access to data management for backups
By accessing data management for program backups via an Industrial Internet of Things (IIoT) platform, important programming data and settings can be regularly backed up and restored. This ensures efficient data protection and simplifies the maintenance of the robot application.
Advantages of this feature in practice
- Minimization of production downtime through rapid restoration of backup data.
- Increased operational reliability through regular data backups.
- Simplified migration of settings and programs between different robots.
- Reduction of errors and inefficiencies through centralized storage of data and programs.
Access to mobile Internet (optional)
Using a SIM card with mobile internet access allows a robot to be controlled independently of the company's network infrastructure. This can be especially useful when, due to structural limitations in the production hall or legal reasons, it is not possible to access the company's online network.
Textual robot programming with JavaScript
Textual robot programming with JavaScript provides an easy-to-learn, flexible, and versatile platform for programming robots. Our robot-specific commands can be easily and quickly implemented in JavaScript. Overall, textual robot programming with JavaScript offers a fast and intuitive way to develop and implement robot applications.
Advantages of textual programming with javascript (horstscript)
- Simplicity: Commands can be easily inserted with just a few clicks, taking advantage of the simplicity of graphical programming.
- Good documentation: The commands are extensively explained and include examples.
- Easy learnability: JavaScript is a widely used and well-documented programming language that is easily accessible and can be quickly learned.
- Flexibility: Textual programming allows for greater flexibility and fine-tuning in the implementation of robotic applications compared to graphical programming.
Manual robot control via digital twin
The manual control of a robot combined with a digital twin allows for direct operation of the robot and verification of its movements within the virtual model. This method is particularly useful during commissioning, maintenance, and troubleshooting, as it offers additional benefits through the use of the digital twin.
Advantages of Manual control of the robot with a digital twin
- Easy commissioning: Manual control simplifies the setup and positioning of the robot during commissioning by using the virtual model as a reference.
- Maintenance and troubleshooting: By directly operating the robot and verifying movements in the digital twin, potential issues can be quickly identified and resolved without affecting the real robot.
- User-friendliness: The intuitive handling of the robot and visualization within the digital twin enable users without programming knowledge to control and verify robot movements.
- Risk reduction: The digital twin helps reduce the risk of damage to the real robot and its environment by detecting potential collisions or misalignments within the virtual model.
- Increased efficiency: By combining manual control and the digital twin, adjustments and optimizations can be performed quickly without the need for time-consuming programming or testing on the real robot.
Extended safety functions
For many robotic applications, it is necessary to comply with the Machinery Directive (2006/42/EC) and other relevant safety standards. Implementing advanced safety features, including redundant safety inputs and outputs, helps to meet the requirements of these directives and ensures the safe operation of robotic applications.
Key safety standards for robotic applications to comply with the Machinery Directive:
- ISO 10218-1/-2: These standards establish safety requirements for industrial robots and robot cells to minimize potential hazards to the operator and the environment.
- ISO/TS 15066: This technical specification outlines safety requirements for collaborative robot applications, where robots and humans work together in the same workspace.
- IEC 62061 / ISO 13849-1: These standards define the basic requirements for the functional safety of machinery and safety-related control systems.
Complying with these and other relevant safety standards is crucial to ensure the safe operation of robotic applications and meet the requirements of the Machinery Directive. Advanced safety features, including redundant safety inputs and outputs, play an essential role in ensuring the safety of users and the environment while meeting regulatory requirements.
Recording process data
The feature "Recording data for process data analysis" enables robots to collect detailed information about their performance and environment during their operations. This collected data can then be analyzed and used to optimize robot operation and programming.
dvantages of recording data for process data analysis
- Troubleshooting: The recorded data can be used to identify and, if necessary, fix errors in robot operation.
- Predictive maintenance: The recorded data can help monitor the robot's condition and plan maintenance work proactively.
- Quality assurance: Analyzing the process data allows for controlling and ensuring the quality of the robot's work.
- Process optimization: The collected data can be used to analyze production processes and identify potential improvements.
Load-dependent optimization of robot speed at waypoints
The "Load-dependent optimization of robot speed at waypoints" feature in articulated arm robots allows for more efficient robot movement based on the weight of the load. This function optimizes the robot's speed and acceleration to achieve higher productivity.
Maximum Robot Speed, Accuracy, and Performance
The overall speed of a robot depends on the speed of each individual axis. The faster a robot can move, the more productive it can be. The accuracy of an industrial robot defines its ability to execute precise and repeatable positioning within specified tolerances. The performance of an industrial robot refers to the combination of speed, accuracy, and payload capacity required for efficient task execution.
Benefits of high robot speed
- Shorter cycle times
- Increased production capacity
- Optimization of production processes
- Improved competitiveness
Benefits of high accuracy
- Consistent product quality
- Minimization of waste and rework
- Better compliance with tolerance requirements
- Higher customer satisfaction
Benefits of high overall performance
- Efficient and effective task execution
- Ability to handle demanding processes
- Increased overall productivity
Setting up a workspace limitation
The "workspace limitation" feature allows for defining limits on a robot's range of motion in robot programming. By effectively restricting the robot's workspace, its safety and efficiency are increased.
Advantages of setting up workspace boundaries in robot programming:
- Increased safety: Workspace boundaries prevent the robot from entering dangerous or undesired areas, reducing the risk of collisions with people or other machines.
- Protection of sensitive areas: By setting boundaries, sensitive areas or elements, such as electronic devices or delicate workpieces, can be protected from unintentional contact by the robot.
- Improved efficiency: Workspace boundaries can help ensure the robot only operates within the relevant area, avoiding unnecessary movements and reducing cycle time.
Contact via the Online Service System
The online service system for the Digital Robot HORST enables efficient communication between users and customer service. It provides quick and easy access to information and solutions for potential issues.
Simulation of robot applications on operator panel
This feature allows the operator to simulate and test a robot application before it is executed on the actual robot. This offers many benefits such as increased efficiency, reduced errors, cost savings, and increased flexibility.
Benefits of simulating robot applications on the control panel:
- Increased efficiency: Simulating potential problems and errors before implementation saves time and resources, thus increasing efficiency.
- Reduced errors: Testing the application before implementation helps avoid errors and reduces the likelihood of malfunctions.
- Cost savings: Avoiding malfunctions and the reduced need for test runs can save costs on repairs and maintenance.
- Increased flexibility: Simulations allow operators to test various scenarios and settings without making physical changes to the robot, making it easier to adapt the application to new requirements.
Communication with periphery via TCP/IP
The HORST intelligent industrial robot communicates with peripheral devices via TCP/IP. The standardized communication protocol TCP/IP 100-Mbit/s Ethernet (sockets) is used, which works on the basis of Ethernet technology and enables data exchange between devices within a network. The advantage of such communication between the robot and the production environment lies in the fast, secure and flexible networking of the systems, which leads to more efficient operations and improved processes.
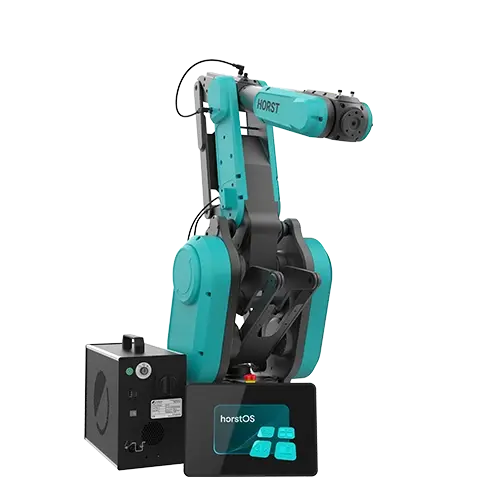
Range
The range refers to the workspace a robot can cover and is therefore crucial for its efficient use in manufacturing. Smaller ranges are ideal for assembly and pick-and-place tasks, while larger ones are suitable for applications such as welding or material handling. Very large ranges are used for handling heavy loads.
Maximum payload
The maximum payload of industrial robots refers to the maximum weight a robot can safely handle and move. It is a critical parameter to ensure the performance and safety of robots in industrial applications.
Application examples for maximum payloads
- Light payload (up to 10 kg): Pick-and-place robots in assembly lines, for example in electronics manufacturing.
- Medium payload (10-100 kg): Welding or painting robots in the automotive industry or machine manufacturing.
- Heavy payload (over 100 kg): Palletizing robots and lifting devices in warehousing and logistics applications, or robots handling heavy vehicle parts in the automotive industry.
Repeatability
The repeatability of industrial robots refers to the robot's ability to perform the same task precisely and reliably multiple times. High repeatability minimizes production errors and contributes to the optimization of processes. High-performance industrial robots are characterized by a repeatability of up to ±0.1 mm.
Maximum Speed (TCP)
The maximum speed (TCP) of industrial robots defines the time it takes to perform a task. A higher speed allows for processing more parts in a shorter time, increasing production throughput. High-performance industrial robots have a maximum speed of at least 3 m/s.
Advantages of higher maximum speeds:
- Increased productivity: A robot with a higher speed can process more parts within a given time frame, thereby increasing production output.
- Shorter cycle times: Faster movements can accelerate process workflows, leading to shorter cycle times and improved machine availability.
- More efficient resource utilization: A higher maximum speed allows for accomplishing the same work with fewer robots or maximizing the use of robots in a shorter time, resulting in more efficient investment and resource utilization.
- Faster return on investment (ROI): Since a higher speed leads to increased productivity, the investment in the robot can be recouped more quickly.
Axis
The number of axis in industrial robots indicates how many degrees of freedom they have, determining their flexibility and versatility in performing tasks. A higher number of axis allows for more complex movements and precise work in different spatial planes. In the industry, 6-axis robots are most common, as they offer particularly high flexibility and precision in their operation.
Weight
The weight of industrial robots affects their flexibility and applicability in manufacturing and production environments. A lower weight can facilitate the adaptation and integration of robots into existing systems, as well as accelerate the transition between different application areas.
Advantages of specific weight classes of robots
- 30 kg: Very lightweight and easy to transport, ideal for quick integration into assembly lines and applications with limited space.
- 60 kg: Offers a good balance between lightness and performance, enabling use in a wider range of applications and making transport and commissioning easier compared to heavier robots.
- 150 kg: This weight class allows for deployment in more demanding tasks that require higher payloads, while the robot remains lighter and easier to handle than very heavy industrial robots.
Ambient temperature
The ambient temperature is significant for industrial robots as it can affect their performance, reliability, and component lifespan. Ideally, industrial robots should operate in environments with moderate temperatures, typically between 5°C and 40°C (40°F and 100°F), to ensure optimal performance and longevity.
Sound level
The sound level of industrial robots indicates how loud the noises are that they produce during their operation. This value is measured in decibels (dB) and serves as an indicator of noise pollution in a production environment. Low sound levels in the range of under 70 dB correspond to a conversation at normal volume.
Protection class
The Ingress Protection (IP) rating of industrial robots indicates the extent to which they are protected against the intrusion of dust, solid objects, and water. The two digits in the IP classification represent the protection against solid objects (first digit) and water (second digit).
Power supply
The power supply of industrial robots is defined by the electrical power in watts (W), as well as the voltage (VAC) and frequency (Hz). Typical power supplies for industrial robots range from 200-600 VAC and 50-60 Hz, with larger robots requiring more power and thus having a higher energy consumption.
Digital inputs on tool flangeThe number of digital inputs for the tool flange of an industrial robot indicates how many digital signals can be received from a tool. These signals can include control commands that influence the operation of the tool. |
Digital outputs on tool flange
The number of digital outputs for the tool flange of an industrial robot indicates how many digital signals can be sent from a tool to the robot. These signals can be control commands for the robot or other components of the production process that should respond to the tool.
I/O power supply on tool flange
The power supply at the tool flange serves to operate tools, sensors, and actuators at the end of the robot arm. Typically, 24-volt voltage is used, while the current strength (amperage) varies depending on the requirements. Lower amperage values enable higher energy efficiency, reduced heat generation, lower cooling requirements, and cost savings through smaller cable cross-sections and lighter components.
Dimensions Control
The control cabinet of an industrial robot is designed to house the robot's control unit, containing all necessary electrical components and the programmable logic controller (PLC). More compact and space-saving solutions are useful, as they can be more easily integrated into existing production environments.
Digital inputs on switch cabinet
The number of digital inputs on the control cabinet of an industrial robot indicates how many signals from external sensors or devices can be received simultaneously. In industrial robotics, 16 to 32 digital inputs are common.
I/O power supply on switchThe power supply for the control of an industrial robot provides electrical energy to the control unit, motors, and sensors. Common voltage levels are 24 or 48 volts. Lower current values (single-digit amperage) have a positive impact on energy efficiency and cooling requirements, leading to cost savings. |
Safety-relevant Inputs (2 channels)Safety-relevant inputs with two channels on industrial robots ensure a high level of safety for the operation and protection of operators and equipment in accordance with DIN EN ISO 10218. The redundant arrangement reduces the risk of malfunctions, since both channels must match in order to recognize a signal as valid. The standard is intended to ensure that industrial robots function reliably and safely in critical situations in order to prevent accidents. |
Wiring between robot and controllerIndustrial robots are connected to their control units through multi-conductor cables that transmit both power supply and data and control signals. The length of the cable should provide enough slack for the robot's movements without causing tension or damage to the cable. |
Digital outputs on switch cabinet
The number of digital outputs on the control cabinet of an industrial robot indicates how many actuators and devices the robot can control. The digital outputs allow the robot to send signals to external devices such as valves, switches, or actuators to perform complex tasks. In industrial robotics, 18 outputs are a common number.
Safety-relevant output (2 channels)
Safety-relevant outputs with two channels on industrial robots are used in accordance with DIN EN ISO 10218 to ensure the safety of operators and equipment by sending redundant control signals to safety-critical components. The dual-channel architecture minimizes the risk of malfunctions, as both channels must match for a valid signal. When the standard is met, an industrial robot can operate reliably and safely even in critical situations.
Dimensions Panel
The dimensions of a control panel for industrial robots with graphical programming affect the user-friendliness and handling of the system. The overall size should provide a balanced combination of ergonomics and functionality.
Display specificationThe display for an industrial robot's operator panel should be high-resolution (for example, Full HD) and large enough to clearly and appealingly display details. A touchscreen is advantageous, as it allows for user-friendly operation, similar to that of a tablet or smartphone. |
Safety relevant emergency stopEmergency stop switches for industrial robots are mandatory to ensure safety in the workspace and minimize the risk of injuries. They work by immediately stopping the robot and interrupting the power supply to the motors when activated, resulting in an instant stop. |
Wiring between panel and controlThe control of industrial robots is connected to the operator panel via cable to transmit data and control signals. The length of the cable should be sufficient to allow comfortable operation of the panel and ensure the operator's freedom of movement. |
Safety relevant three-level enabling switch
Multi-stage enable switches for robot operation are mandatory because they provide an additional level of safety during manual control. They prevent unintentional movements or dangerous situations. If the enable switch is released while in manual mode, the robot's movement stops immediately.
Graphical programming on the panel
The graphical programming on the control panel provides a user-friendly interface for easily controlling robot movements and functions, even without extensive programming knowledge. This promotes efficient, adaptable control and directly improves productivity and efficiency at the facility.
Advantages of graphical programming on the panel:
- User-friendliness: An intuitive graphical user interface allows even individuals without programming knowledge to operate and adapt the robot. This promotes broader acceptance and usage of the robot.
- Efficiency improvement: Graphical programming enables tasks to be programmed and optimized more quickly and easily, leading to higher productivity and efficiency.
- Error minimization: The graphical user interface supports the detection and correction of programming errors, reducing the risk of errors that can lead to production downtime or damage to equipment.
- Cost savings: The simple programming and error correction save the company time and resources, resulting in a reduction of operational and maintenance costs.
- Flexibility: Graphical programming allows for quick adaptation and modification of robot functions to respond to changing production requirements. This increases the robot's flexibility and enables versatile usage in various application areas.
Access to licence management and Updates
Access to license management and updates allows for centralized management of robot software licenses and wireless updates. This keeps the robot control system up to date and ensures it continues to meet operational requirements in the future.
Advantages of this feature in practice
- The wireless installation of software updates and patches without manual intervention saves valuable work time and increases efficiency.
- Central management and monitoring of software licenses for all robots in the fleet reduces administrative effort and simplifies control over the entire robot inventory.
- Regular updates to the robot software can fix any defects and further improve the robot's performance after purchase, reducing the risk of production disruptions or failures.
- By accessing the latest features and improvements in the software, companies benefit from over-the-air technological advancements and the continuous development of the robots.
Access to data management for backups
By accessing data management for program backups via an Industrial Internet of Things (IIoT) platform, important programming data and settings can be regularly backed up and restored. This ensures efficient data protection and simplifies the maintenance of the robot application.
Advantages of this feature in practice
- Minimization of production downtime through rapid restoration of backup data.
- Increased operational reliability through regular data backups.
- Simplified migration of settings and programs between different robots.
- Reduction of errors and inefficiencies through centralized storage of data and programs.
Access to mobile Internet (optional)
Using a SIM card with mobile internet access allows a robot to be controlled independently of the company's network infrastructure. This can be especially useful when, due to structural limitations in the production hall or legal reasons, it is not possible to access the company's online network.
Textual robot programming with JavaScript
Textual robot programming with JavaScript provides an easy-to-learn, flexible, and versatile platform for programming robots. Our robot-specific commands can be easily and quickly implemented in JavaScript. Overall, textual robot programming with JavaScript offers a fast and intuitive way to develop and implement robot applications.
Advantages of textual programming with javascript (horstscript)
- Simplicity: Commands can be easily inserted with just a few clicks, taking advantage of the simplicity of graphical programming.
- Good documentation: The commands are extensively explained and include examples.
- Easy learnability: JavaScript is a widely used and well-documented programming language that is easily accessible and can be quickly learned.
- Flexibility: Textual programming allows for greater flexibility and fine-tuning in the implementation of robotic applications compared to graphical programming.
Manual robot control via digital twin
The manual control of a robot combined with a digital twin allows for direct operation of the robot and verification of its movements within the virtual model. This method is particularly useful during commissioning, maintenance, and troubleshooting, as it offers additional benefits through the use of the digital twin.
Advantages of Manual control of the robot with a digital twin
- Easy commissioning: Manual control simplifies the setup and positioning of the robot during commissioning by using the virtual model as a reference.
- Maintenance and troubleshooting: By directly operating the robot and verifying movements in the digital twin, potential issues can be quickly identified and resolved without affecting the real robot.
- User-friendliness: The intuitive handling of the robot and visualization within the digital twin enable users without programming knowledge to control and verify robot movements.
- Risk reduction: The digital twin helps reduce the risk of damage to the real robot and its environment by detecting potential collisions or misalignments within the virtual model.
- Increased efficiency: By combining manual control and the digital twin, adjustments and optimizations can be performed quickly without the need for time-consuming programming or testing on the real robot.
Extended safety functions
For many robotic applications, it is necessary to comply with the Machinery Directive (2006/42/EC) and other relevant safety standards. Implementing advanced safety features, including redundant safety inputs and outputs, helps to meet the requirements of these directives and ensures the safe operation of robotic applications.
Key safety standards for robotic applications to comply with the Machinery Directive:
- ISO 10218-1/-2: These standards establish safety requirements for industrial robots and robot cells to minimize potential hazards to the operator and the environment.
- ISO/TS 15066: This technical specification outlines safety requirements for collaborative robot applications, where robots and humans work together in the same workspace.
- IEC 62061 / ISO 13849-1: These standards define the basic requirements for the functional safety of machinery and safety-related control systems.
Complying with these and other relevant safety standards is crucial to ensure the safe operation of robotic applications and meet the requirements of the Machinery Directive. Advanced safety features, including redundant safety inputs and outputs, play an essential role in ensuring the safety of users and the environment while meeting regulatory requirements.
Recording process data
The feature "Recording data for process data analysis" enables robots to collect detailed information about their performance and environment during their operations. This collected data can then be analyzed and used to optimize robot operation and programming.
dvantages of recording data for process data analysis
- Troubleshooting: The recorded data can be used to identify and, if necessary, fix errors in robot operation.
- Predictive maintenance: The recorded data can help monitor the robot's condition and plan maintenance work proactively.
- Quality assurance: Analyzing the process data allows for controlling and ensuring the quality of the robot's work.
- Process optimization: The collected data can be used to analyze production processes and identify potential improvements.
Load-dependent optimization of robot speed at waypoints
The "Load-dependent optimization of robot speed at waypoints" feature in articulated arm robots allows for more efficient robot movement based on the weight of the load. This function optimizes the robot's speed and acceleration to achieve higher productivity.
Maximum Robot Speed, Accuracy, and Performance
The overall speed of a robot depends on the speed of each individual axis. The faster a robot can move, the more productive it can be. The accuracy of an industrial robot defines its ability to execute precise and repeatable positioning within specified tolerances. The performance of an industrial robot refers to the combination of speed, accuracy, and payload capacity required for efficient task execution.
Benefits of high robot speed
- Shorter cycle times
- Increased production capacity
- Optimization of production processes
- Improved competitiveness
Benefits of high accuracy
- Consistent product quality
- Minimization of waste and rework
- Better compliance with tolerance requirements
- Higher customer satisfaction
Benefits of high overall performance
- Efficient and effective task execution
- Ability to handle demanding processes
- Increased overall productivity
Setting up a workspace limitation
The "workspace limitation" feature allows for defining limits on a robot's range of motion in robot programming. By effectively restricting the robot's workspace, its safety and efficiency are increased.
Advantages of setting up workspace boundaries in robot programming:
- Increased safety: Workspace boundaries prevent the robot from entering dangerous or undesired areas, reducing the risk of collisions with people or other machines.
- Protection of sensitive areas: By setting boundaries, sensitive areas or elements, such as electronic devices or delicate workpieces, can be protected from unintentional contact by the robot.
- Improved efficiency: Workspace boundaries can help ensure the robot only operates within the relevant area, avoiding unnecessary movements and reducing cycle time.
Contact via the Online Service System
The online service system for the Digital Robot HORST enables efficient communication between users and customer service. It provides quick and easy access to information and solutions for potential issues.
Simulation of robot applications on operator panel
This feature allows the operator to simulate and test a robot application before it is executed on the actual robot. This offers many benefits such as increased efficiency, reduced errors, cost savings, and increased flexibility.
Benefits of simulating robot applications on the control panel:
- Increased efficiency: Simulating potential problems and errors before implementation saves time and resources, thus increasing efficiency.
- Reduced errors: Testing the application before implementation helps avoid errors and reduces the likelihood of malfunctions.
- Cost savings: Avoiding malfunctions and the reduced need for test runs can save costs on repairs and maintenance.
- Increased flexibility: Simulations allow operators to test various scenarios and settings without making physical changes to the robot, making it easier to adapt the application to new requirements.
Communication with periphery via TCP/IP
The HORST intelligent industrial robot communicates with peripheral devices via TCP/IP. The standardized communication protocol TCP/IP 100-Mbit/s Ethernet (sockets) is used, which works on the basis of Ethernet technology and enables data exchange between devices within a network. The advantage of such communication between the robot and the production environment lies in the fast, secure and flexible networking of the systems, which leads to more efficient operations and improved processes.
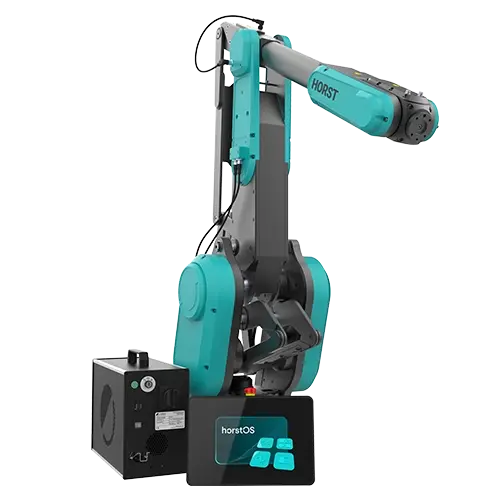
Range
The range refers to the workspace a robot can cover and is therefore crucial for its efficient use in manufacturing. Smaller ranges are ideal for assembly and pick-and-place tasks, while larger ones are suitable for applications such as welding or material handling. Very large ranges are used for handling heavy loads.
Maximum payload
The maximum payload of industrial robots refers to the maximum weight a robot can safely handle and move. It is a critical parameter to ensure the performance and safety of robots in industrial applications.
Application examples for maximum payloads
- Light payload (up to 10 kg): Pick-and-place robots in assembly lines, for example in electronics manufacturing.
- Medium payload (10-100 kg): Welding or painting robots in the automotive industry or machine manufacturing.
- Heavy payload (over 100 kg): Palletizing robots and lifting devices in warehousing and logistics applications, or robots handling heavy vehicle parts in the automotive industry.
Repeatability
The repeatability of industrial robots refers to the robot's ability to perform the same task precisely and reliably multiple times. High repeatability minimizes production errors and contributes to the optimization of processes. High-performance industrial robots are characterized by a repeatability of up to ±0.1 mm.
Maximum Speed (TCP)
The maximum speed (TCP) of industrial robots defines the time it takes to perform a task. A higher speed allows for processing more parts in a shorter time, increasing production throughput. High-performance industrial robots have a maximum speed of at least 3 m/s.
Advantages of higher maximum speeds:
- Increased productivity: A robot with a higher speed can process more parts within a given time frame, thereby increasing production output.
- Shorter cycle times: Faster movements can accelerate process workflows, leading to shorter cycle times and improved machine availability.
- More efficient resource utilization: A higher maximum speed allows for accomplishing the same work with fewer robots or maximizing the use of robots in a shorter time, resulting in more efficient investment and resource utilization.
- Faster return on investment (ROI): Since a higher speed leads to increased productivity, the investment in the robot can be recouped more quickly.
Axis
The number of axis in industrial robots indicates how many degrees of freedom they have, determining their flexibility and versatility in performing tasks. A higher number of axis allows for more complex movements and precise work in different spatial planes. In the industry, 6-axis robots are most common, as they offer particularly high flexibility and precision in their operation.
Weight
The weight of industrial robots affects their flexibility and applicability in manufacturing and production environments. A lower weight can facilitate the adaptation and integration of robots into existing systems, as well as accelerate the transition between different application areas.
Advantages of specific weight classes of robots
- 30 kg: Very lightweight and easy to transport, ideal for quick integration into assembly lines and applications with limited space.
- 60 kg: Offers a good balance between lightness and performance, enabling use in a wider range of applications and making transport and commissioning easier compared to heavier robots.
- 150 kg: This weight class allows for deployment in more demanding tasks that require higher payloads, while the robot remains lighter and easier to handle than very heavy industrial robots.
Ambient temperature
The ambient temperature is significant for industrial robots as it can affect their performance, reliability, and component lifespan. Ideally, industrial robots should operate in environments with moderate temperatures, typically between 5°C and 40°C (40°F and 100°F), to ensure optimal performance and longevity.
Sound level
The sound level of industrial robots indicates how loud the noises are that they produce during their operation. This value is measured in decibels (dB) and serves as an indicator of noise pollution in a production environment. Low sound levels in the range of under 70 dB correspond to a conversation at normal volume.
Protection class
The Ingress Protection (IP) rating of industrial robots indicates the extent to which they are protected against the intrusion of dust, solid objects, and water. The two digits in the IP classification represent the protection against solid objects (first digit) and water (second digit).
Power supply
The power supply of industrial robots is defined by the electrical power in watts (W), as well as the voltage (VAC) and frequency (Hz). Typical power supplies for industrial robots range from 200-600 VAC and 50-60 Hz, with larger robots requiring more power and thus having a higher energy consumption.
Digital inputs on tool flangeThe number of digital inputs for the tool flange of an industrial robot indicates how many digital signals can be received from a tool. These signals can include control commands that influence the operation of the tool. |
Digital outputs on tool flange
The number of digital outputs for the tool flange of an industrial robot indicates how many digital signals can be sent from a tool to the robot. These signals can be control commands for the robot or other components of the production process that should respond to the tool.
I/O power supply on tool flange
The power supply at the tool flange serves to operate tools, sensors, and actuators at the end of the robot arm. Typically, 24-volt voltage is used, while the current strength (amperage) varies depending on the requirements. Lower amperage values enable higher energy efficiency, reduced heat generation, lower cooling requirements, and cost savings through smaller cable cross-sections and lighter components.
Dimensions Control
The control cabinet of an industrial robot is designed to house the robot's control unit, containing all necessary electrical components and the programmable logic controller (PLC). More compact and space-saving solutions are useful, as they can be more easily integrated into existing production environments.
Digital inputs on switch cabinet
The number of digital inputs on the control cabinet of an industrial robot indicates how many signals from external sensors or devices can be received simultaneously. In industrial robotics, 16 to 32 digital inputs are common.
I/O power supply on switchThe power supply for the control of an industrial robot provides electrical energy to the control unit, motors, and sensors. Common voltage levels are 24 or 48 volts. Lower current values (single-digit amperage) have a positive impact on energy efficiency and cooling requirements, leading to cost savings. |
Safety-relevant Inputs (2 channels)Safety-relevant inputs with two channels on industrial robots ensure a high level of safety for the operation and protection of operators and equipment in accordance with DIN EN ISO 10218. The redundant arrangement reduces the risk of malfunctions, since both channels must match in order to recognize a signal as valid. The standard is intended to ensure that industrial robots function reliably and safely in critical situations in order to prevent accidents. |
Wiring between robot and controllerIndustrial robots are connected to their control units through multi-conductor cables that transmit both power supply and data and control signals. The length of the cable should provide enough slack for the robot's movements without causing tension or damage to the cable. |
Digital outputs on switch cabinet
The number of digital outputs on the control cabinet of an industrial robot indicates how many actuators and devices the robot can control. The digital outputs allow the robot to send signals to external devices such as valves, switches, or actuators to perform complex tasks. In industrial robotics, 18 outputs are a common number.
Safety-relevant output (2 channels)
Safety-relevant outputs with two channels on industrial robots are used in accordance with DIN EN ISO 10218 to ensure the safety of operators and equipment by sending redundant control signals to safety-critical components. The dual-channel architecture minimizes the risk of malfunctions, as both channels must match for a valid signal. When the standard is met, an industrial robot can operate reliably and safely even in critical situations.
Dimensions Panel
The dimensions of a control panel for industrial robots with graphical programming affect the user-friendliness and handling of the system. The overall size should provide a balanced combination of ergonomics and functionality.
Display specificationThe display for an industrial robot's operator panel should be high-resolution (for example, Full HD) and large enough to clearly and appealingly display details. A touchscreen is advantageous, as it allows for user-friendly operation, similar to that of a tablet or smartphone. |
Safety relevant emergency stopEmergency stop switches for industrial robots are mandatory to ensure safety in the workspace and minimize the risk of injuries. They work by immediately stopping the robot and interrupting the power supply to the motors when activated, resulting in an instant stop. |
Wiring between panel and controlThe control of industrial robots is connected to the operator panel via cable to transmit data and control signals. The length of the cable should be sufficient to allow comfortable operation of the panel and ensure the operator's freedom of movement. |
Safety relevant three-level enabling switch
Multi-stage enable switches for robot operation are mandatory because they provide an additional level of safety during manual control. They prevent unintentional movements or dangerous situations. If the enable switch is released while in manual mode, the robot's movement stops immediately.
Graphical programming on the panel
The graphical programming on the control panel provides a user-friendly interface for easily controlling robot movements and functions, even without extensive programming knowledge. This promotes efficient, adaptable control and directly improves productivity and efficiency at the facility.
Advantages of graphical programming on the panel:
- User-friendliness: An intuitive graphical user interface allows even individuals without programming knowledge to operate and adapt the robot. This promotes broader acceptance and usage of the robot.
- Efficiency improvement: Graphical programming enables tasks to be programmed and optimized more quickly and easily, leading to higher productivity and efficiency.
- Error minimization: The graphical user interface supports the detection and correction of programming errors, reducing the risk of errors that can lead to production downtime or damage to equipment.
- Cost savings: The simple programming and error correction save the company time and resources, resulting in a reduction of operational and maintenance costs.
- Flexibility: Graphical programming allows for quick adaptation and modification of robot functions to respond to changing production requirements. This increases the robot's flexibility and enables versatile usage in various application areas.
Access to licence management and Updates
Access to license management and updates allows for centralized management of robot software licenses and wireless updates. This keeps the robot control system up to date and ensures it continues to meet operational requirements in the future.
Advantages of this feature in practice
- The wireless installation of software updates and patches without manual intervention saves valuable work time and increases efficiency.
- Central management and monitoring of software licenses for all robots in the fleet reduces administrative effort and simplifies control over the entire robot inventory.
- Regular updates to the robot software can fix any defects and further improve the robot's performance after purchase, reducing the risk of production disruptions or failures.
- By accessing the latest features and improvements in the software, companies benefit from over-the-air technological advancements and the continuous development of the robots.
Access to data management for backups
By accessing data management for program backups via an Industrial Internet of Things (IIoT) platform, important programming data and settings can be regularly backed up and restored. This ensures efficient data protection and simplifies the maintenance of the robot application.
Advantages of this feature in practice
- Minimization of production downtime through rapid restoration of backup data.
- Increased operational reliability through regular data backups.
- Simplified migration of settings and programs between different robots.
- Reduction of errors and inefficiencies through centralized storage of data and programs.
Access to mobile Internet (optional)
Using a SIM card with mobile internet access allows a robot to be controlled independently of the company's network infrastructure. This can be especially useful when, due to structural limitations in the production hall or legal reasons, it is not possible to access the company's online network.
Textual robot programming with JavaScript
Textual robot programming with JavaScript provides an easy-to-learn, flexible, and versatile platform for programming robots. Our robot-specific commands can be easily and quickly implemented in JavaScript. Overall, textual robot programming with JavaScript offers a fast and intuitive way to develop and implement robot applications.
Advantages of textual programming with javascript (horstscript)
- Simplicity: Commands can be easily inserted with just a few clicks, taking advantage of the simplicity of graphical programming.
- Good documentation: The commands are extensively explained and include examples.
- Easy learnability: JavaScript is a widely used and well-documented programming language that is easily accessible and can be quickly learned.
- Flexibility: Textual programming allows for greater flexibility and fine-tuning in the implementation of robotic applications compared to graphical programming.
Manual robot control via digital twin
The manual control of a robot combined with a digital twin allows for direct operation of the robot and verification of its movements within the virtual model. This method is particularly useful during commissioning, maintenance, and troubleshooting, as it offers additional benefits through the use of the digital twin.
Advantages of Manual control of the robot with a digital twin
- Easy commissioning: Manual control simplifies the setup and positioning of the robot during commissioning by using the virtual model as a reference.
- Maintenance and troubleshooting: By directly operating the robot and verifying movements in the digital twin, potential issues can be quickly identified and resolved without affecting the real robot.
- User-friendliness: The intuitive handling of the robot and visualization within the digital twin enable users without programming knowledge to control and verify robot movements.
- Risk reduction: The digital twin helps reduce the risk of damage to the real robot and its environment by detecting potential collisions or misalignments within the virtual model.
- Increased efficiency: By combining manual control and the digital twin, adjustments and optimizations can be performed quickly without the need for time-consuming programming or testing on the real robot.
Extended safety functions
For many robotic applications, it is necessary to comply with the Machinery Directive (2006/42/EC) and other relevant safety standards. Implementing advanced safety features, including redundant safety inputs and outputs, helps to meet the requirements of these directives and ensures the safe operation of robotic applications.
Key safety standards for robotic applications to comply with the Machinery Directive:
- ISO 10218-1/-2: These standards establish safety requirements for industrial robots and robot cells to minimize potential hazards to the operator and the environment.
- ISO/TS 15066: This technical specification outlines safety requirements for collaborative robot applications, where robots and humans work together in the same workspace.
- IEC 62061 / ISO 13849-1: These standards define the basic requirements for the functional safety of machinery and safety-related control systems.
Complying with these and other relevant safety standards is crucial to ensure the safe operation of robotic applications and meet the requirements of the Machinery Directive. Advanced safety features, including redundant safety inputs and outputs, play an essential role in ensuring the safety of users and the environment while meeting regulatory requirements.
Recording process data
The feature "Recording data for process data analysis" enables robots to collect detailed information about their performance and environment during their operations. This collected data can then be analyzed and used to optimize robot operation and programming.
dvantages of recording data for process data analysis
- Troubleshooting: The recorded data can be used to identify and, if necessary, fix errors in robot operation.
- Predictive maintenance: The recorded data can help monitor the robot's condition and plan maintenance work proactively.
- Quality assurance: Analyzing the process data allows for controlling and ensuring the quality of the robot's work.
- Process optimization: The collected data can be used to analyze production processes and identify potential improvements.
Load-dependent optimization of robot speed at waypoints
The "Load-dependent optimization of robot speed at waypoints" feature in articulated arm robots allows for more efficient robot movement based on the weight of the load. This function optimizes the robot's speed and acceleration to achieve higher productivity.
Maximum Robot Speed, Accuracy, and Performance
The overall speed of a robot depends on the speed of each individual axis. The faster a robot can move, the more productive it can be. The accuracy of an industrial robot defines its ability to execute precise and repeatable positioning within specified tolerances. The performance of an industrial robot refers to the combination of speed, accuracy, and payload capacity required for efficient task execution.
Benefits of high robot speed
- Shorter cycle times
- Increased production capacity
- Optimization of production processes
- Improved competitiveness
Benefits of high accuracy
- Consistent product quality
- Minimization of waste and rework
- Better compliance with tolerance requirements
- Higher customer satisfaction
Benefits of high overall performance
- Efficient and effective task execution
- Ability to handle demanding processes
- Increased overall productivity
Setting up a workspace limitation
The "workspace limitation" feature allows for defining limits on a robot's range of motion in robot programming. By effectively restricting the robot's workspace, its safety and efficiency are increased.
Advantages of setting up workspace boundaries in robot programming:
- Increased safety: Workspace boundaries prevent the robot from entering dangerous or undesired areas, reducing the risk of collisions with people or other machines.
- Protection of sensitive areas: By setting boundaries, sensitive areas or elements, such as electronic devices or delicate workpieces, can be protected from unintentional contact by the robot.
- Improved efficiency: Workspace boundaries can help ensure the robot only operates within the relevant area, avoiding unnecessary movements and reducing cycle time.
Contact via the Online Service System
The online service system for the Digital Robot HORST enables efficient communication between users and customer service. It provides quick and easy access to information and solutions for potential issues.
Simulation of robot applications on operator panel
This feature allows the operator to simulate and test a robot application before it is executed on the actual robot. This offers many benefits such as increased efficiency, reduced errors, cost savings, and increased flexibility.
Benefits of simulating robot applications on the control panel:
- Increased efficiency: Simulating potential problems and errors before implementation saves time and resources, thus increasing efficiency.
- Reduced errors: Testing the application before implementation helps avoid errors and reduces the likelihood of malfunctions.
- Cost savings: Avoiding malfunctions and the reduced need for test runs can save costs on repairs and maintenance.
- Increased flexibility: Simulations allow operators to test various scenarios and settings without making physical changes to the robot, making it easier to adapt the application to new requirements.
Communication with periphery via TCP/IP
The HORST intelligent industrial robot communicates with peripheral devices via TCP/IP. The standardized communication protocol TCP/IP 100-Mbit/s Ethernet (sockets) is used, which works on the basis of Ethernet technology and enables data exchange between devices within a network. The advantage of such communication between the robot and the production environment lies in the fast, secure and flexible networking of the systems, which leads to more efficient operations and improved processes.
Range
The range refers to the workspace a robot can cover and is therefore crucial for its efficient use in manufacturing. Smaller ranges are ideal for assembly and pick-and-place tasks, while larger ones are suitable for applications such as welding or material handling. Very large ranges are used for handling heavy loads.
Maximum payload
The maximum payload of industrial robots refers to the maximum weight a robot can safely handle and move. It is a critical parameter to ensure the performance and safety of robots in industrial applications.
Application examples for maximum payloads
- Light payload (up to 10 kg): Pick-and-place robots in assembly lines, for example in electronics manufacturing.
- Medium payload (10-100 kg): Welding or painting robots in the automotive industry or machine manufacturing.
- Heavy payload (over 100 kg): Palletizing robots and lifting devices in warehousing and logistics applications, or robots handling heavy vehicle parts in the automotive industry.
Repeatability
The repeatability of industrial robots refers to the robot's ability to perform the same task precisely and reliably multiple times. High repeatability minimizes production errors and contributes to the optimization of processes. High-performance industrial robots are characterized by a repeatability of up to ±0.1 mm.
Maximum Speed (TCP)
The maximum speed (TCP) of industrial robots defines the time it takes to perform a task. A higher speed allows for processing more parts in a shorter time, increasing production throughput. High-performance industrial robots have a maximum speed of at least 3 m/s.
Advantages of higher maximum speeds:
- Increased productivity: A robot with a higher speed can process more parts within a given time frame, thereby increasing production output.
- Shorter cycle times: Faster movements can accelerate process workflows, leading to shorter cycle times and improved machine availability.
- More efficient resource utilization: A higher maximum speed allows for accomplishing the same work with fewer robots or maximizing the use of robots in a shorter time, resulting in more efficient investment and resource utilization.
- Faster return on investment (ROI): Since a higher speed leads to increased productivity, the investment in the robot can be recouped more quickly.
Axis
The number of axis in industrial robots indicates how many degrees of freedom they have, determining their flexibility and versatility in performing tasks. A higher number of axis allows for more complex movements and precise work in different spatial planes. In the industry, 6-axis robots are most common, as they offer particularly high flexibility and precision in their operation.
Weight
The weight of industrial robots affects their flexibility and applicability in manufacturing and production environments. A lower weight can facilitate the adaptation and integration of robots into existing systems, as well as accelerate the transition between different application areas.
Advantages of specific weight classes of robots
- 30 kg: Very lightweight and easy to transport, ideal for quick integration into assembly lines and applications with limited space.
- 60 kg: Offers a good balance between lightness and performance, enabling use in a wider range of applications and making transport and commissioning easier compared to heavier robots.
- 150 kg: This weight class allows for deployment in more demanding tasks that require higher payloads, while the robot remains lighter and easier to handle than very heavy industrial robots.
Ambient temperature
The ambient temperature is significant for industrial robots as it can affect their performance, reliability, and component lifespan. Ideally, industrial robots should operate in environments with moderate temperatures, typically between 5°C and 40°C (40°F and 100°F), to ensure optimal performance and longevity.
Sound level
The sound level of industrial robots indicates how loud the noises are that they produce during their operation. This value is measured in decibels (dB) and serves as an indicator of noise pollution in a production environment. Low sound levels in the range of under 70 dB correspond to a conversation at normal volume.
Protection class
The Ingress Protection (IP) rating of industrial robots indicates the extent to which they are protected against the intrusion of dust, solid objects, and water. The two digits in the IP classification represent the protection against solid objects (first digit) and water (second digit).
Power supply
The power supply of industrial robots is defined by the electrical power in watts (W), as well as the voltage (VAC) and frequency (Hz). Typical power supplies for industrial robots range from 200-600 VAC and 50-60 Hz, with larger robots requiring more power and thus having a higher energy consumption.
Digital inputs on tool flangeThe number of digital inputs for the tool flange of an industrial robot indicates how many digital signals can be received from a tool. These signals can include control commands that influence the operation of the tool. |
Digital outputs on tool flange
The number of digital outputs for the tool flange of an industrial robot indicates how many digital signals can be sent from a tool to the robot. These signals can be control commands for the robot or other components of the production process that should respond to the tool.
I/O power supply on tool flange
The power supply at the tool flange serves to operate tools, sensors, and actuators at the end of the robot arm. Typically, 24-volt voltage is used, while the current strength (amperage) varies depending on the requirements. Lower amperage values enable higher energy efficiency, reduced heat generation, lower cooling requirements, and cost savings through smaller cable cross-sections and lighter components.
Dimensions Control
The control cabinet of an industrial robot is designed to house the robot's control unit, containing all necessary electrical components and the programmable logic controller (PLC). More compact and space-saving solutions are useful, as they can be more easily integrated into existing production environments.
Digital inputs on switch cabinet
The number of digital inputs on the control cabinet of an industrial robot indicates how many signals from external sensors or devices can be received simultaneously. In industrial robotics, 16 to 32 digital inputs are common.
I/O power supply on switchThe power supply for the control of an industrial robot provides electrical energy to the control unit, motors, and sensors. Common voltage levels are 24 or 48 volts. Lower current values (single-digit amperage) have a positive impact on energy efficiency and cooling requirements, leading to cost savings. |
Safety-relevant Inputs (2 channels)Safety-relevant inputs with two channels on industrial robots ensure a high level of safety for the operation and protection of operators and equipment in accordance with DIN EN ISO 10218. The redundant arrangement reduces the risk of malfunctions, since both channels must match in order to recognize a signal as valid. The standard is intended to ensure that industrial robots function reliably and safely in critical situations in order to prevent accidents. |
Wiring between robot and controllerIndustrial robots are connected to their control units through multi-conductor cables that transmit both power supply and data and control signals. The length of the cable should provide enough slack for the robot's movements without causing tension or damage to the cable. |
Digital outputs on switch cabinet
The number of digital outputs on the control cabinet of an industrial robot indicates how many actuators and devices the robot can control. The digital outputs allow the robot to send signals to external devices such as valves, switches, or actuators to perform complex tasks. In industrial robotics, 18 outputs are a common number.
Safety-relevant output (2 channels)
Safety-relevant outputs with two channels on industrial robots are used in accordance with DIN EN ISO 10218 to ensure the safety of operators and equipment by sending redundant control signals to safety-critical components. The dual-channel architecture minimizes the risk of malfunctions, as both channels must match for a valid signal. When the standard is met, an industrial robot can operate reliably and safely even in critical situations.
Dimensions Panel
The dimensions of a control panel for industrial robots with graphical programming affect the user-friendliness and handling of the system. The overall size should provide a balanced combination of ergonomics and functionality.
Display specificationThe display for an industrial robot's operator panel should be high-resolution (for example, Full HD) and large enough to clearly and appealingly display details. A touchscreen is advantageous, as it allows for user-friendly operation, similar to that of a tablet or smartphone. |
Safety relevant emergency stopEmergency stop switches for industrial robots are mandatory to ensure safety in the workspace and minimize the risk of injuries. They work by immediately stopping the robot and interrupting the power supply to the motors when activated, resulting in an instant stop. |
Wiring between panel and controlThe control of industrial robots is connected to the operator panel via cable to transmit data and control signals. The length of the cable should be sufficient to allow comfortable operation of the panel and ensure the operator's freedom of movement. |
Safety relevant three-level enabling switch
Multi-stage enable switches for robot operation are mandatory because they provide an additional level of safety during manual control. They prevent unintentional movements or dangerous situations. If the enable switch is released while in manual mode, the robot's movement stops immediately.
Graphical programming on the panel
The graphical programming on the control panel provides a user-friendly interface for easily controlling robot movements and functions, even without extensive programming knowledge. This promotes efficient, adaptable control and directly improves productivity and efficiency at the facility.
Advantages of graphical programming on the panel:
- User-friendliness: An intuitive graphical user interface allows even individuals without programming knowledge to operate and adapt the robot. This promotes broader acceptance and usage of the robot.
- Efficiency improvement: Graphical programming enables tasks to be programmed and optimized more quickly and easily, leading to higher productivity and efficiency.
- Error minimization: The graphical user interface supports the detection and correction of programming errors, reducing the risk of errors that can lead to production downtime or damage to equipment.
- Cost savings: The simple programming and error correction save the company time and resources, resulting in a reduction of operational and maintenance costs.
- Flexibility: Graphical programming allows for quick adaptation and modification of robot functions to respond to changing production requirements. This increases the robot's flexibility and enables versatile usage in various application areas.
Access to licence management and Updates
Access to license management and updates allows for centralized management of robot software licenses and wireless updates. This keeps the robot control system up to date and ensures it continues to meet operational requirements in the future.
Advantages of this feature in practice
- The wireless installation of software updates and patches without manual intervention saves valuable work time and increases efficiency.
- Central management and monitoring of software licenses for all robots in the fleet reduces administrative effort and simplifies control over the entire robot inventory.
- Regular updates to the robot software can fix any defects and further improve the robot's performance after purchase, reducing the risk of production disruptions or failures.
- By accessing the latest features and improvements in the software, companies benefit from over-the-air technological advancements and the continuous development of the robots.
Access to data management for backups
By accessing data management for program backups via an Industrial Internet of Things (IIoT) platform, important programming data and settings can be regularly backed up and restored. This ensures efficient data protection and simplifies the maintenance of the robot application.
Advantages of this feature in practice
- Minimization of production downtime through rapid restoration of backup data.
- Increased operational reliability through regular data backups.
- Simplified migration of settings and programs between different robots.
- Reduction of errors and inefficiencies through centralized storage of data and programs.
Access to mobile Internet (optional)
Using a SIM card with mobile internet access allows a robot to be controlled independently of the company's network infrastructure. This can be especially useful when, due to structural limitations in the production hall or legal reasons, it is not possible to access the company's online network.
Textual robot programming with JavaScript
Textual robot programming with JavaScript provides an easy-to-learn, flexible, and versatile platform for programming robots. Our robot-specific commands can be easily and quickly implemented in JavaScript. Overall, textual robot programming with JavaScript offers a fast and intuitive way to develop and implement robot applications.
Advantages of textual programming with javascript (horstscript)
- Simplicity: Commands can be easily inserted with just a few clicks, taking advantage of the simplicity of graphical programming.
- Good documentation: The commands are extensively explained and include examples.
- Easy learnability: JavaScript is a widely used and well-documented programming language that is easily accessible and can be quickly learned.
- Flexibility: Textual programming allows for greater flexibility and fine-tuning in the implementation of robotic applications compared to graphical programming.
Manual robot control via digital twin
The manual control of a robot combined with a digital twin allows for direct operation of the robot and verification of its movements within the virtual model. This method is particularly useful during commissioning, maintenance, and troubleshooting, as it offers additional benefits through the use of the digital twin.
Advantages of Manual control of the robot with a digital twin
- Easy commissioning: Manual control simplifies the setup and positioning of the robot during commissioning by using the virtual model as a reference.
- Maintenance and troubleshooting: By directly operating the robot and verifying movements in the digital twin, potential issues can be quickly identified and resolved without affecting the real robot.
- User-friendliness: The intuitive handling of the robot and visualization within the digital twin enable users without programming knowledge to control and verify robot movements.
- Risk reduction: The digital twin helps reduce the risk of damage to the real robot and its environment by detecting potential collisions or misalignments within the virtual model.
- Increased efficiency: By combining manual control and the digital twin, adjustments and optimizations can be performed quickly without the need for time-consuming programming or testing on the real robot.
Extended safety functions
For many robotic applications, it is necessary to comply with the Machinery Directive (2006/42/EC) and other relevant safety standards. Implementing advanced safety features, including redundant safety inputs and outputs, helps to meet the requirements of these directives and ensures the safe operation of robotic applications.
Key safety standards for robotic applications to comply with the Machinery Directive:
- ISO 10218-1/-2: These standards establish safety requirements for industrial robots and robot cells to minimize potential hazards to the operator and the environment.
- ISO/TS 15066: This technical specification outlines safety requirements for collaborative robot applications, where robots and humans work together in the same workspace.
- IEC 62061 / ISO 13849-1: These standards define the basic requirements for the functional safety of machinery and safety-related control systems.
Complying with these and other relevant safety standards is crucial to ensure the safe operation of robotic applications and meet the requirements of the Machinery Directive. Advanced safety features, including redundant safety inputs and outputs, play an essential role in ensuring the safety of users and the environment while meeting regulatory requirements.
Recording process data
The feature "Recording data for process data analysis" enables robots to collect detailed information about their performance and environment during their operations. This collected data can then be analyzed and used to optimize robot operation and programming.
dvantages of recording data for process data analysis
- Troubleshooting: The recorded data can be used to identify and, if necessary, fix errors in robot operation.
- Predictive maintenance: The recorded data can help monitor the robot's condition and plan maintenance work proactively.
- Quality assurance: Analyzing the process data allows for controlling and ensuring the quality of the robot's work.
- Process optimization: The collected data can be used to analyze production processes and identify potential improvements.
Load-dependent optimization of robot speed at waypoints
The "Load-dependent optimization of robot speed at waypoints" feature in articulated arm robots allows for more efficient robot movement based on the weight of the load. This function optimizes the robot's speed and acceleration to achieve higher productivity.
Maximum Robot Speed, Accuracy, and Performance
The overall speed of a robot depends on the speed of each individual axis. The faster a robot can move, the more productive it can be. The accuracy of an industrial robot defines its ability to execute precise and repeatable positioning within specified tolerances. The performance of an industrial robot refers to the combination of speed, accuracy, and payload capacity required for efficient task execution.
Benefits of high robot speed
- Shorter cycle times
- Increased production capacity
- Optimization of production processes
- Improved competitiveness
Benefits of high accuracy
- Consistent product quality
- Minimization of waste and rework
- Better compliance with tolerance requirements
- Higher customer satisfaction
Benefits of high overall performance
- Efficient and effective task execution
- Ability to handle demanding processes
- Increased overall productivity
Setting up a workspace limitation
The "workspace limitation" feature allows for defining limits on a robot's range of motion in robot programming. By effectively restricting the robot's workspace, its safety and efficiency are increased.
Advantages of setting up workspace boundaries in robot programming:
- Increased safety: Workspace boundaries prevent the robot from entering dangerous or undesired areas, reducing the risk of collisions with people or other machines.
- Protection of sensitive areas: By setting boundaries, sensitive areas or elements, such as electronic devices or delicate workpieces, can be protected from unintentional contact by the robot.
- Improved efficiency: Workspace boundaries can help ensure the robot only operates within the relevant area, avoiding unnecessary movements and reducing cycle time.
Contact via the Online Service System
The online service system for the Digital Robot HORST enables efficient communication between users and customer service. It provides quick and easy access to information and solutions for potential issues.
Simulation of robot applications on operator panel
This feature allows the operator to simulate and test a robot application before it is executed on the actual robot. This offers many benefits such as increased efficiency, reduced errors, cost savings, and increased flexibility.
Benefits of simulating robot applications on the control panel:
- Increased efficiency: Simulating potential problems and errors before implementation saves time and resources, thus increasing efficiency.
- Reduced errors: Testing the application before implementation helps avoid errors and reduces the likelihood of malfunctions.
- Cost savings: Avoiding malfunctions and the reduced need for test runs can save costs on repairs and maintenance.
- Increased flexibility: Simulations allow operators to test various scenarios and settings without making physical changes to the robot, making it easier to adapt the application to new requirements.
Communication with periphery via TCP/IP
The HORST intelligent industrial robot communicates with peripheral devices via TCP/IP. The standardized communication protocol TCP/IP 100-Mbit/s Ethernet (sockets) is used, which works on the basis of Ethernet technology and enables data exchange between devices within a network. The advantage of such communication between the robot and the production environment lies in the fast, secure and flexible networking of the systems, which leads to more efficient operations and improved processes.
2. Additional Features
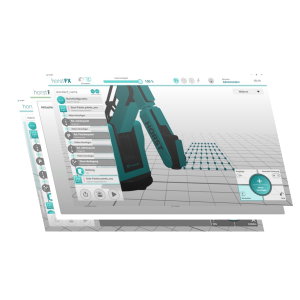
Graphical programming of palletizing applications
The graphical robot programming of palletizing applications allows users to configure and control robot applications through an intuitive, visual user interface. This feature simplifies the programming of palletizing applications and improves the efficiency in carrying out such tasks.
Advantages of graphical programming: palletizing applications:
- User-friendliness: A graphical user interface (GUI) allows users to perform application configuration and control in an easy and intuitive way, without requiring complex programming knowledge.
- Efficiency improvement: Through the visual representation and simple adjustment of palletizing applications, users can work faster and more effectively, leading to higher productivity.
- Error minimization: Graphical programming reduces the likelihood of errors that can occur more frequently in traditional text programming, as users can directly visualize robot movements and actions.
- Cost savings: By simplifying the programming process and reducing errors, companies can save costs on training, troubleshooting, and production downtime.
- Flexibility: Graphical robot programming allows users to quickly and easily adapt palletizing applications to changing requirements or product lines, increasing the robot's flexibility and adaptability.
Graphical robot programming of complex paths
The graphical robot programming of complex paths enables users to program industrial robots easily and intuitively through graphical user interfaces, allowing for precise and efficient execution of complex motion sequences. Robot paths can be visually designed and adjusted directly on the surface without requiring in-depth programming knowledge.
Benefits of graphical programming of complex paths:
- Time savings in programming and setup: Visual design and adjustment of robot paths significantly shorten development and setup times, accelerating production start-ups.
- Easy adaptation to changing production processes: Motion sequences can be quickly and effortlessly modified to respond to changing production requirements without extensive programming work.
- Reduction of training and familiarization times: The intuitive user interface allows even workers without specialized programming knowledge to effectively operate and program the robot, reducing costs for training and familiarization times.
User-defined operating view with makro buttons
The custom control view with macro buttons feature allows users to create individual interfaces with personalized macro buttons. This function simplifies interaction with frequently used commands and increases productivity in various applications.
Advantages of user-defined operating view with makro buttons
- Personalization: Customize the interface to suit individual needs and working styles.
- Efficiency: Quicker access to frequently used commands and functions.
- Productivity boost: Time savings and optimized workflows by reducing clicks and menu navigation.
- Flexibility: Easily add, remove, or change macro buttons as needed.
User-defined coordinate systems
The "Custom Coordinate Systems" feature allows for defining and using individual reference frames within a robotic application. These coordinate systems enable precise positioning and alignment of the robot, as well as efficient collaboration with other systems.
Advantages of user-defined coordinate systems
- Orientation: Improves the robot's orientation in complex environments by providing local reference frames for different parts of the workspace.
- Collaboration: Facilitates collaboration between multiple robots or systems by using common coordinate systems.
- Flexibility: Simplifies the integration of new features or adaptations to changing production requirements through the adaptability of coordinate systems.
- Simplification: Makes programming easier by allowing the use of multiple coordinate systems for different tasks or tools.
Access to the Profinet interface
Profinet is a modern, Ethernet-based protocol designed for real-time communication and data exchange between automation components in industrial networks. When robots have the appropriate interface, they can be more efficiently controlled in connection with other automation components and integrated into complex production processes.
Advantages of the profinet interface
-
Fast response time: In a machine loading system, for example, an industrial robot with a Profinet interface can adjust its movements in real-time to the speed of the conveyor belt, ensuring that parts are placed precisely and without delay.
-
Flexibility: Through communication with other machines, a robot can be more easily integrated into an existing production line using the Profinet interface.
-
Scalability: In a dosing application, such as filling liquids into bottles, the Profinet interface allows the networking of multiple robots and machines to ensure uniform and precise dosing across all bottles and increase production capacity.
-
Diagnostics: Remote monitoring of an industrial robot is made possible by the Profinet interface, allowing for faster error correction. For example, when the robot is used for sorting parts, if one of the parts is sorted incorrectly.
-
Energy efficiency: With a Profinet interface, the robot's energy consumption can be optimized by, for example, switching to an energy-saving mode during standby times.
Access to the modbus interface
Modbus is a widely-used, serial communication protocol that enables the connection of industrial electronic devices, such as sensors, actuators, and controllers. In the field of automation, Modbus is used for communication and coordination between robots and other machines.
Advantages of the modbus interface
-
Easy integration: Due to the widespread use of Modbus in the industry, it is easy to integrate an industrial robot with a Modbus interface into existing systems and machines without having to make extensive adjustments.
-
Cost efficiency: Modbus is a cost-effective communication protocol that does not incur expensive hardware or licensing costs, making it attractive for companies with limited budgets.
-
Open protocol: As Modbus is an open protocol, devices from different manufacturers can communicate with each other without issues, which expands the selection of compatible devices and systems.
-
Simple troubleshooting and maintenance: By using Modbus, industrial robots can relay information about their operating status to higher-level control systems. This allows for easier troubleshooting and maintenance, as potential disruptions can be detected and addressed early on.
Primary interface for external function callsThe feature "Access to the primary interface for executing external function calls" enables a robot to access external functions and execute them within its program flow. XML-RPC is used as the primary interface, allowing the robot to function as a "slave" and be controlled by an external device, the "master". |
|
![]() |
|
Benefits of the primary interface:
|
AI Copilot
Benefit from the best context-sensitive real-time support. Program more efficiently through AI optimization of programs and AI-assisted creation of program modules and functions
Your advantages:
- Maximum time & cost efficiency in support: Questions & assistance without support calls - with the AI Copilot you receive context-sensitive answers in real time. So you can continue quickly, even if you encounter problems when creating programmes.
- Your personal trainer: Further training through sparring with the AI Copilot, just like with a trainer, application or service technician.
AI Programming
Support in the creation of complex programmes
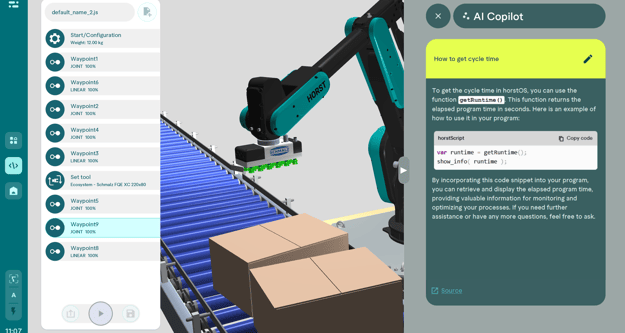
Your advantages of AI Programming
- Most efficient programming: AI generation of functions, programme modules and programme templates
- Optimisation and correction of programs: Syntax analysis and output of optimisation options
AI Error Handling
The AI Copilot goes beyond simple fault detection.
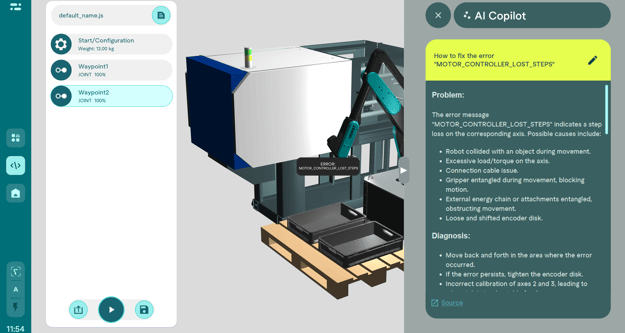
Your advantages of AI Error Handling
- Comprehensive analysis in the event of an error: It analyses your project setup, your program logic and even your hardware configurations to determine the cause of problems. It then provides actionable recommendations and potential solutions, saving you valuable time and frustration.
- Transfer error messages directly to the co-pilot: If an error message occurs, it can be transferred directly to the AI Copilot for analysis.
Component Management
Advantages of centralised component management
- Simple creation of components: Quick step-by-step setup and configuration of connected components
- Single point of control: Direct access to the component interface. Enormous time savings through setup, operation and making adjustments from a central point.
Process Control
Advantages of customised process control
- Simple operation and a good overview: By customising the Process Control, the operator can be provided with exactly the functions they need during operation. This minimises errors caused by incorrect operation
- Flexible set-up: The most important functions (e.g. release door or open gripper) can be made directly accessible in the Process Control.
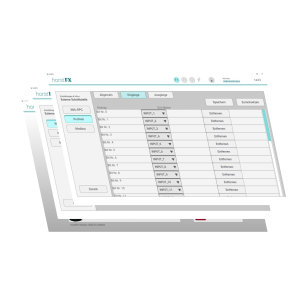
Graphical programming of palletizing applications
The graphical robot programming of palletizing applications allows users to configure and control robot applications through an intuitive, visual user interface. This feature simplifies the programming of palletizing applications and improves the efficiency in carrying out such tasks.
Advantages of graphical programming: palletizing applications:
- User-friendliness: A graphical user interface (GUI) allows users to perform application configuration and control in an easy and intuitive way, without requiring complex programming knowledge.
- Efficiency improvement: Through the visual representation and simple adjustment of palletizing applications, users can work faster and more effectively, leading to higher productivity.
- Error minimization: Graphical programming reduces the likelihood of errors that can occur more frequently in traditional text programming, as users can directly visualize robot movements and actions.
- Cost savings: By simplifying the programming process and reducing errors, companies can save costs on training, troubleshooting, and production downtime.
- Flexibility: Graphical robot programming allows users to quickly and easily adapt palletizing applications to changing requirements or product lines, increasing the robot's flexibility and adaptability.
Graphical robot programming of complex paths
The graphical robot programming of complex paths enables users to program industrial robots easily and intuitively through graphical user interfaces, allowing for precise and efficient execution of complex motion sequences. Robot paths can be visually designed and adjusted directly on the surface without requiring in-depth programming knowledge.
Benefits of graphical programming of complex paths:
- Time savings in programming and setup: Visual design and adjustment of robot paths significantly shorten development and setup times, accelerating production start-ups.
- Easy adaptation to changing production processes: Motion sequences can be quickly and effortlessly modified to respond to changing production requirements without extensive programming work.
- Reduction of training and familiarization times: The intuitive user interface allows even workers without specialized programming knowledge to effectively operate and program the robot, reducing costs for training and familiarization times.
User-defined operating view with makro buttons
The custom control view with macro buttons feature allows users to create individual interfaces with personalized macro buttons. This function simplifies interaction with frequently used commands and increases productivity in various applications.
Advantages of user-defined operating view with makro buttons
- Personalization: Customize the interface to suit individual needs and working styles.
- Efficiency: Quicker access to frequently used commands and functions.
- Productivity boost: Time savings and optimized workflows by reducing clicks and menu navigation.
- Flexibility: Easily add, remove, or change macro buttons as needed.
User-defined coordinate systems
The "Custom Coordinate Systems" feature allows for defining and using individual reference frames within a robotic application. These coordinate systems enable precise positioning and alignment of the robot, as well as efficient collaboration with other systems.
Advantages of user-defined coordinate systems
- Orientation: Improves the robot's orientation in complex environments by providing local reference frames for different parts of the workspace.
- Collaboration: Facilitates collaboration between multiple robots or systems by using common coordinate systems.
- Flexibility: Simplifies the integration of new features or adaptations to changing production requirements through the adaptability of coordinate systems.
- Simplification: Makes programming easier by allowing the use of multiple coordinate systems for different tasks or tools.
Access to the Profinet interface
Profinet is a modern, Ethernet-based protocol designed for real-time communication and data exchange between automation components in industrial networks. When robots have the appropriate interface, they can be more efficiently controlled in connection with other automation components and integrated into complex production processes.
Advantages of the profinet interface
-
Fast response time: In a machine loading system, for example, an industrial robot with a Profinet interface can adjust its movements in real-time to the speed of the conveyor belt, ensuring that parts are placed precisely and without delay.
-
Flexibility: Through communication with other machines, a robot can be more easily integrated into an existing production line using the Profinet interface.
-
Scalability: In a dosing application, such as filling liquids into bottles, the Profinet interface allows the networking of multiple robots and machines to ensure uniform and precise dosing across all bottles and increase production capacity.
-
Diagnostics: Remote monitoring of an industrial robot is made possible by the Profinet interface, allowing for faster error correction. For example, when the robot is used for sorting parts, if one of the parts is sorted incorrectly.
-
Energy efficiency: With a Profinet interface, the robot's energy consumption can be optimized by, for example, switching to an energy-saving mode during standby times.
Access to the modbus interface
Modbus is a widely-used, serial communication protocol that enables the connection of industrial electronic devices, such as sensors, actuators, and controllers. In the field of automation, Modbus is used for communication and coordination between robots and other machines.
Advantages of the modbus interface
-
Easy integration: Due to the widespread use of Modbus in the industry, it is easy to integrate an industrial robot with a Modbus interface into existing systems and machines without having to make extensive adjustments.
-
Cost efficiency: Modbus is a cost-effective communication protocol that does not incur expensive hardware or licensing costs, making it attractive for companies with limited budgets.
-
Open protocol: As Modbus is an open protocol, devices from different manufacturers can communicate with each other without issues, which expands the selection of compatible devices and systems.
-
Simple troubleshooting and maintenance: By using Modbus, industrial robots can relay information about their operating status to higher-level control systems. This allows for easier troubleshooting and maintenance, as potential disruptions can be detected and addressed early on.
Primary interface for external function callsThe feature "Access to the primary interface for executing external function calls" enables a robot to access external functions and execute them within its program flow. XML-RPC is used as the primary interface, allowing the robot to function as a "slave" and be controlled by an external device, the "master". |
|
![]() |
|
Benefits of the primary interface:
|
AI Copilot
Benefit from the best context-sensitive real-time support. Program more efficiently through AI optimization of programs and AI-assisted creation of program modules and functions
Your advantages:
- Maximum time & cost efficiency in support: Questions & assistance without support calls - with the AI Copilot you receive context-sensitive answers in real time. So you can continue quickly, even if you encounter problems when creating programmes.
- Your personal trainer: Further training through sparring with the AI Copilot, just like with a trainer, application or service technician.
AI Programming
Support in the creation of complex programmes
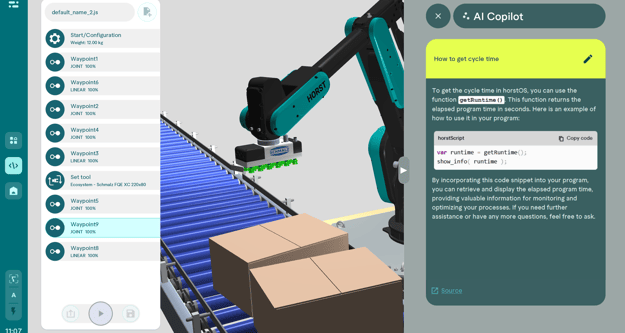
Your advantages of AI Programming
- Most efficient programming: AI generation of functions, programme modules and programme templates
- Optimisation and correction of programs: Syntax analysis and output of optimisation options
AI Error Handling
The AI Copilot goes beyond simple fault detection.
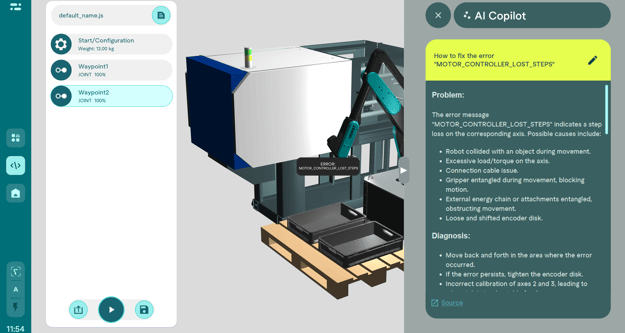
Your advantages of AI Error Handling
- Comprehensive analysis in the event of an error: It analyses your project setup, your program logic and even your hardware configurations to determine the cause of problems. It then provides actionable recommendations and potential solutions, saving you valuable time and frustration.
- Transfer error messages directly to the co-pilot: If an error message occurs, it can be transferred directly to the AI Copilot for analysis.
Component Management
Advantages of centralised component management
- Simple creation of components: Quick step-by-step setup and configuration of connected components
- Single point of control: Direct access to the component interface. Enormous time savings through setup, operation and making adjustments from a central point.
Process Control
Advantages of customised process control
- Simple operation and a good overview: By customising the Process Control, the operator can be provided with exactly the functions they need during operation. This minimises errors caused by incorrect operation
- Flexible set-up: The most important functions (e.g. release door or open gripper) can be made directly accessible in the Process Control.
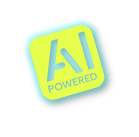
Graphical programming of palletizing applications
The graphical robot programming of palletizing applications allows users to configure and control robot applications through an intuitive, visual user interface. This feature simplifies the programming of palletizing applications and improves the efficiency in carrying out such tasks.
Advantages of graphical programming: palletizing applications:
- User-friendliness: A graphical user interface (GUI) allows users to perform application configuration and control in an easy and intuitive way, without requiring complex programming knowledge.
- Efficiency improvement: Through the visual representation and simple adjustment of palletizing applications, users can work faster and more effectively, leading to higher productivity.
- Error minimization: Graphical programming reduces the likelihood of errors that can occur more frequently in traditional text programming, as users can directly visualize robot movements and actions.
- Cost savings: By simplifying the programming process and reducing errors, companies can save costs on training, troubleshooting, and production downtime.
- Flexibility: Graphical robot programming allows users to quickly and easily adapt palletizing applications to changing requirements or product lines, increasing the robot's flexibility and adaptability.
Graphical robot programming of complex paths
The graphical robot programming of complex paths enables users to program industrial robots easily and intuitively through graphical user interfaces, allowing for precise and efficient execution of complex motion sequences. Robot paths can be visually designed and adjusted directly on the surface without requiring in-depth programming knowledge.
Benefits of graphical programming of complex paths:
- Time savings in programming and setup: Visual design and adjustment of robot paths significantly shorten development and setup times, accelerating production start-ups.
- Easy adaptation to changing production processes: Motion sequences can be quickly and effortlessly modified to respond to changing production requirements without extensive programming work.
- Reduction of training and familiarization times: The intuitive user interface allows even workers without specialized programming knowledge to effectively operate and program the robot, reducing costs for training and familiarization times.
User-defined operating view with makro buttons
The custom control view with macro buttons feature allows users to create individual interfaces with personalized macro buttons. This function simplifies interaction with frequently used commands and increases productivity in various applications.
Advantages of user-defined operating view with makro buttons
- Personalization: Customize the interface to suit individual needs and working styles.
- Efficiency: Quicker access to frequently used commands and functions.
- Productivity boost: Time savings and optimized workflows by reducing clicks and menu navigation.
- Flexibility: Easily add, remove, or change macro buttons as needed.
User-defined coordinate systems
The "Custom Coordinate Systems" feature allows for defining and using individual reference frames within a robotic application. These coordinate systems enable precise positioning and alignment of the robot, as well as efficient collaboration with other systems.
Advantages of user-defined coordinate systems
- Orientation: Improves the robot's orientation in complex environments by providing local reference frames for different parts of the workspace.
- Collaboration: Facilitates collaboration between multiple robots or systems by using common coordinate systems.
- Flexibility: Simplifies the integration of new features or adaptations to changing production requirements through the adaptability of coordinate systems.
- Simplification: Makes programming easier by allowing the use of multiple coordinate systems for different tasks or tools.
Access to the Profinet interface
Profinet is a modern, Ethernet-based protocol designed for real-time communication and data exchange between automation components in industrial networks. When robots have the appropriate interface, they can be more efficiently controlled in connection with other automation components and integrated into complex production processes.
Advantages of the profinet interface
-
Fast response time: In a machine loading system, for example, an industrial robot with a Profinet interface can adjust its movements in real-time to the speed of the conveyor belt, ensuring that parts are placed precisely and without delay.
-
Flexibility: Through communication with other machines, a robot can be more easily integrated into an existing production line using the Profinet interface.
-
Scalability: In a dosing application, such as filling liquids into bottles, the Profinet interface allows the networking of multiple robots and machines to ensure uniform and precise dosing across all bottles and increase production capacity.
-
Diagnostics: Remote monitoring of an industrial robot is made possible by the Profinet interface, allowing for faster error correction. For example, when the robot is used for sorting parts, if one of the parts is sorted incorrectly.
-
Energy efficiency: With a Profinet interface, the robot's energy consumption can be optimized by, for example, switching to an energy-saving mode during standby times.
Access to the modbus interface
Modbus is a widely-used, serial communication protocol that enables the connection of industrial electronic devices, such as sensors, actuators, and controllers. In the field of automation, Modbus is used for communication and coordination between robots and other machines.
Advantages of the modbus interface
-
Easy integration: Due to the widespread use of Modbus in the industry, it is easy to integrate an industrial robot with a Modbus interface into existing systems and machines without having to make extensive adjustments.
-
Cost efficiency: Modbus is a cost-effective communication protocol that does not incur expensive hardware or licensing costs, making it attractive for companies with limited budgets.
-
Open protocol: As Modbus is an open protocol, devices from different manufacturers can communicate with each other without issues, which expands the selection of compatible devices and systems.
-
Simple troubleshooting and maintenance: By using Modbus, industrial robots can relay information about their operating status to higher-level control systems. This allows for easier troubleshooting and maintenance, as potential disruptions can be detected and addressed early on.
Primary interface for external function callsThe feature "Access to the primary interface for executing external function calls" enables a robot to access external functions and execute them within its program flow. XML-RPC is used as the primary interface, allowing the robot to function as a "slave" and be controlled by an external device, the "master". |
|
![]() |
|
Benefits of the primary interface:
|
AI Copilot
Benefit from the best context-sensitive real-time support. Program more efficiently through AI optimization of programs and AI-assisted creation of program modules and functions
Your advantages:
- Maximum time & cost efficiency in support: Questions & assistance without support calls - with the AI Copilot you receive context-sensitive answers in real time. So you can continue quickly, even if you encounter problems when creating programmes.
- Your personal trainer: Further training through sparring with the AI Copilot, just like with a trainer, application or service technician.
AI Programming
Support in the creation of complex programmes
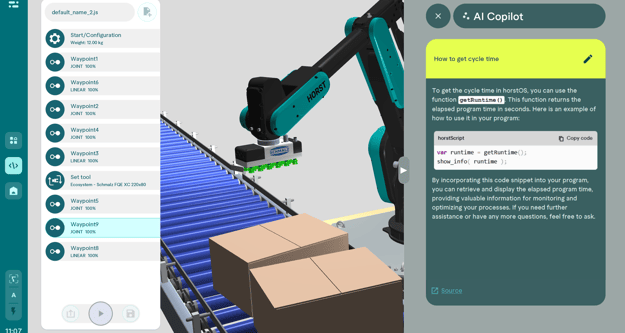
Your advantages of AI Programming
- Most efficient programming: AI generation of functions, programme modules and programme templates
- Optimisation and correction of programs: Syntax analysis and output of optimisation options
AI Error Handling
The AI Copilot goes beyond simple fault detection.
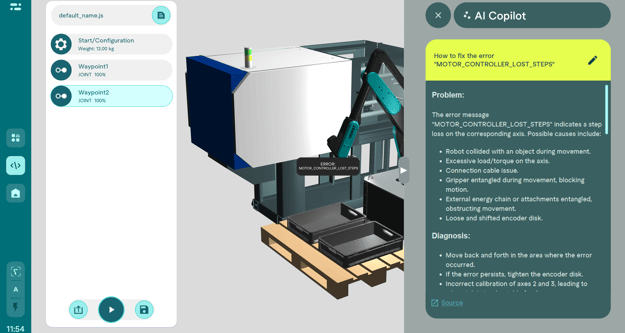
Your advantages of AI Error Handling
- Comprehensive analysis in the event of an error: It analyses your project setup, your program logic and even your hardware configurations to determine the cause of problems. It then provides actionable recommendations and potential solutions, saving you valuable time and frustration.
- Transfer error messages directly to the co-pilot: If an error message occurs, it can be transferred directly to the AI Copilot for analysis.
Component Management
Advantages of centralised component management
- Simple creation of components: Quick step-by-step setup and configuration of connected components
- Single point of control: Direct access to the component interface. Enormous time savings through setup, operation and making adjustments from a central point.
Process Control
Advantages of customised process control
- Simple operation and a good overview: By customising the Process Control, the operator can be provided with exactly the functions they need during operation. This minimises errors caused by incorrect operation
- Flexible set-up: The most important functions (e.g. release door or open gripper) can be made directly accessible in the Process Control.
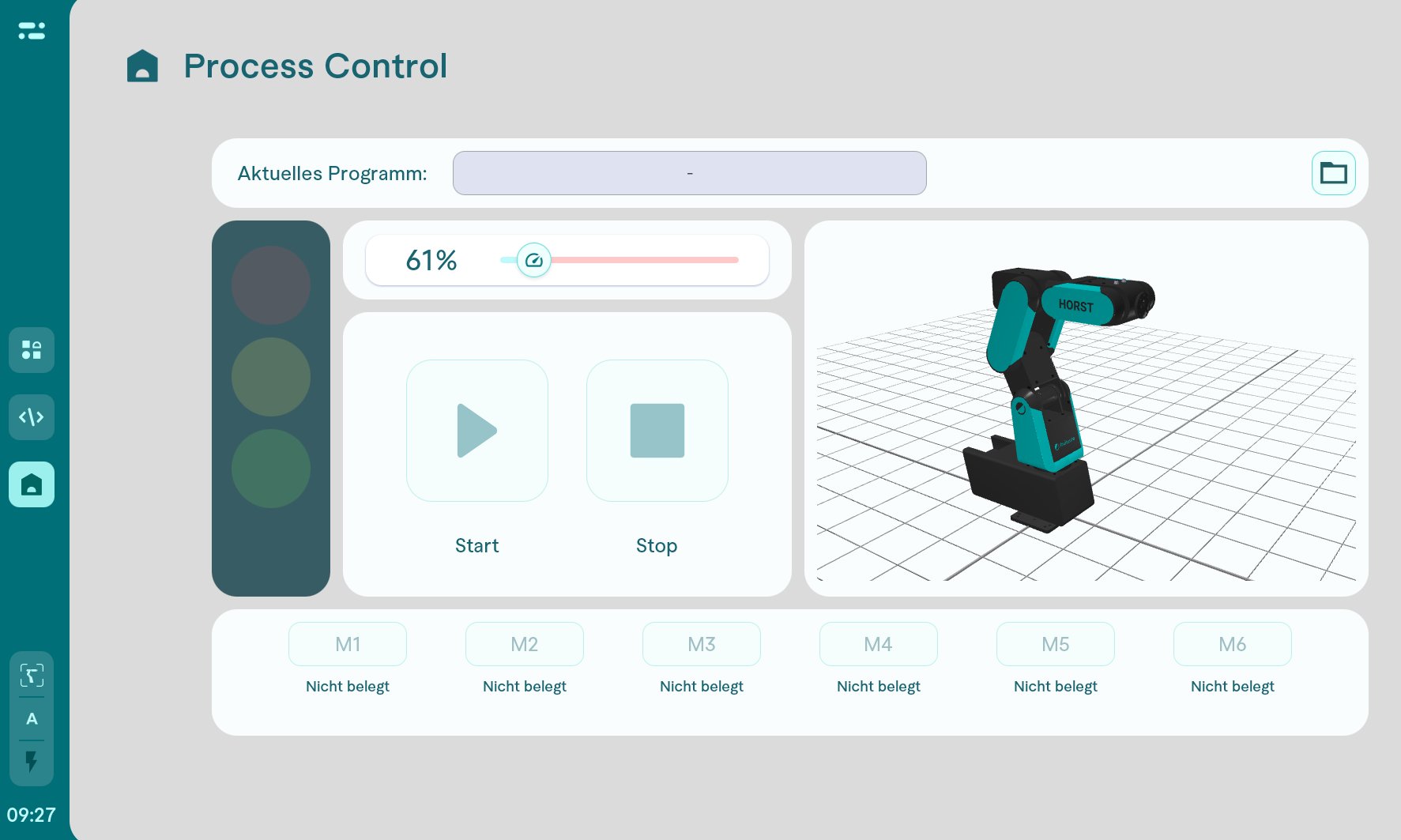
Graphical programming of palletizing applications
The graphical robot programming of palletizing applications allows users to configure and control robot applications through an intuitive, visual user interface. This feature simplifies the programming of palletizing applications and improves the efficiency in carrying out such tasks.
Advantages of graphical programming: palletizing applications:
- User-friendliness: A graphical user interface (GUI) allows users to perform application configuration and control in an easy and intuitive way, without requiring complex programming knowledge.
- Efficiency improvement: Through the visual representation and simple adjustment of palletizing applications, users can work faster and more effectively, leading to higher productivity.
- Error minimization: Graphical programming reduces the likelihood of errors that can occur more frequently in traditional text programming, as users can directly visualize robot movements and actions.
- Cost savings: By simplifying the programming process and reducing errors, companies can save costs on training, troubleshooting, and production downtime.
- Flexibility: Graphical robot programming allows users to quickly and easily adapt palletizing applications to changing requirements or product lines, increasing the robot's flexibility and adaptability.
Graphical robot programming of complex paths
The graphical robot programming of complex paths enables users to program industrial robots easily and intuitively through graphical user interfaces, allowing for precise and efficient execution of complex motion sequences. Robot paths can be visually designed and adjusted directly on the surface without requiring in-depth programming knowledge.
Benefits of graphical programming of complex paths:
- Time savings in programming and setup: Visual design and adjustment of robot paths significantly shorten development and setup times, accelerating production start-ups.
- Easy adaptation to changing production processes: Motion sequences can be quickly and effortlessly modified to respond to changing production requirements without extensive programming work.
- Reduction of training and familiarization times: The intuitive user interface allows even workers without specialized programming knowledge to effectively operate and program the robot, reducing costs for training and familiarization times.
User-defined operating view with makro buttons
The custom control view with macro buttons feature allows users to create individual interfaces with personalized macro buttons. This function simplifies interaction with frequently used commands and increases productivity in various applications.
Advantages of user-defined operating view with makro buttons
- Personalization: Customize the interface to suit individual needs and working styles.
- Efficiency: Quicker access to frequently used commands and functions.
- Productivity boost: Time savings and optimized workflows by reducing clicks and menu navigation.
- Flexibility: Easily add, remove, or change macro buttons as needed.
User-defined coordinate systems
The "Custom Coordinate Systems" feature allows for defining and using individual reference frames within a robotic application. These coordinate systems enable precise positioning and alignment of the robot, as well as efficient collaboration with other systems.
Advantages of user-defined coordinate systems
- Orientation: Improves the robot's orientation in complex environments by providing local reference frames for different parts of the workspace.
- Collaboration: Facilitates collaboration between multiple robots or systems by using common coordinate systems.
- Flexibility: Simplifies the integration of new features or adaptations to changing production requirements through the adaptability of coordinate systems.
- Simplification: Makes programming easier by allowing the use of multiple coordinate systems for different tasks or tools.
Access to the Profinet interface
Profinet is a modern, Ethernet-based protocol designed for real-time communication and data exchange between automation components in industrial networks. When robots have the appropriate interface, they can be more efficiently controlled in connection with other automation components and integrated into complex production processes.
Advantages of the profinet interface
-
Fast response time: In a machine loading system, for example, an industrial robot with a Profinet interface can adjust its movements in real-time to the speed of the conveyor belt, ensuring that parts are placed precisely and without delay.
-
Flexibility: Through communication with other machines, a robot can be more easily integrated into an existing production line using the Profinet interface.
-
Scalability: In a dosing application, such as filling liquids into bottles, the Profinet interface allows the networking of multiple robots and machines to ensure uniform and precise dosing across all bottles and increase production capacity.
-
Diagnostics: Remote monitoring of an industrial robot is made possible by the Profinet interface, allowing for faster error correction. For example, when the robot is used for sorting parts, if one of the parts is sorted incorrectly.
-
Energy efficiency: With a Profinet interface, the robot's energy consumption can be optimized by, for example, switching to an energy-saving mode during standby times.
Access to the modbus interface
Modbus is a widely-used, serial communication protocol that enables the connection of industrial electronic devices, such as sensors, actuators, and controllers. In the field of automation, Modbus is used for communication and coordination between robots and other machines.
Advantages of the modbus interface
-
Easy integration: Due to the widespread use of Modbus in the industry, it is easy to integrate an industrial robot with a Modbus interface into existing systems and machines without having to make extensive adjustments.
-
Cost efficiency: Modbus is a cost-effective communication protocol that does not incur expensive hardware or licensing costs, making it attractive for companies with limited budgets.
-
Open protocol: As Modbus is an open protocol, devices from different manufacturers can communicate with each other without issues, which expands the selection of compatible devices and systems.
-
Simple troubleshooting and maintenance: By using Modbus, industrial robots can relay information about their operating status to higher-level control systems. This allows for easier troubleshooting and maintenance, as potential disruptions can be detected and addressed early on.
Primary interface for external function callsThe feature "Access to the primary interface for executing external function calls" enables a robot to access external functions and execute them within its program flow. XML-RPC is used as the primary interface, allowing the robot to function as a "slave" and be controlled by an external device, the "master". |
|
![]() |
|
Benefits of the primary interface:
|
AI Copilot
Benefit from the best context-sensitive real-time support. Program more efficiently through AI optimization of programs and AI-assisted creation of program modules and functions
Your advantages:
- Maximum time & cost efficiency in support: Questions & assistance without support calls - with the AI Copilot you receive context-sensitive answers in real time. So you can continue quickly, even if you encounter problems when creating programmes.
- Your personal trainer: Further training through sparring with the AI Copilot, just like with a trainer, application or service technician.
AI Programming
Support in the creation of complex programmes
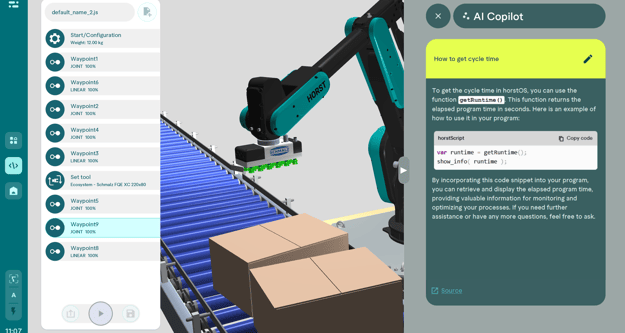
Your advantages of AI Programming
- Most efficient programming: AI generation of functions, programme modules and programme templates
- Optimisation and correction of programs: Syntax analysis and output of optimisation options
AI Error Handling
The AI Copilot goes beyond simple fault detection.
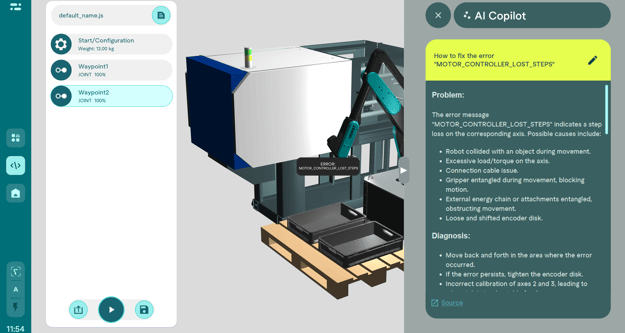
Your advantages of AI Error Handling
- Comprehensive analysis in the event of an error: It analyses your project setup, your program logic and even your hardware configurations to determine the cause of problems. It then provides actionable recommendations and potential solutions, saving you valuable time and frustration.
- Transfer error messages directly to the co-pilot: If an error message occurs, it can be transferred directly to the AI Copilot for analysis.
Component Management
Advantages of centralised component management
- Simple creation of components: Quick step-by-step setup and configuration of connected components
- Single point of control: Direct access to the component interface. Enormous time savings through setup, operation and making adjustments from a central point.
Process Control
Advantages of customised process control
- Simple operation and a good overview: By customising the Process Control, the operator can be provided with exactly the functions they need during operation. This minimises errors caused by incorrect operation
- Flexible set-up: The most important functions (e.g. release door or open gripper) can be made directly accessible in the Process Control.
Graphical programming of palletizing applications
The graphical robot programming of palletizing applications allows users to configure and control robot applications through an intuitive, visual user interface. This feature simplifies the programming of palletizing applications and improves the efficiency in carrying out such tasks.
Advantages of graphical programming: palletizing applications:
- User-friendliness: A graphical user interface (GUI) allows users to perform application configuration and control in an easy and intuitive way, without requiring complex programming knowledge.
- Efficiency improvement: Through the visual representation and simple adjustment of palletizing applications, users can work faster and more effectively, leading to higher productivity.
- Error minimization: Graphical programming reduces the likelihood of errors that can occur more frequently in traditional text programming, as users can directly visualize robot movements and actions.
- Cost savings: By simplifying the programming process and reducing errors, companies can save costs on training, troubleshooting, and production downtime.
- Flexibility: Graphical robot programming allows users to quickly and easily adapt palletizing applications to changing requirements or product lines, increasing the robot's flexibility and adaptability.
Graphical robot programming of complex paths
The graphical robot programming of complex paths enables users to program industrial robots easily and intuitively through graphical user interfaces, allowing for precise and efficient execution of complex motion sequences. Robot paths can be visually designed and adjusted directly on the surface without requiring in-depth programming knowledge.
Benefits of graphical programming of complex paths:
- Time savings in programming and setup: Visual design and adjustment of robot paths significantly shorten development and setup times, accelerating production start-ups.
- Easy adaptation to changing production processes: Motion sequences can be quickly and effortlessly modified to respond to changing production requirements without extensive programming work.
- Reduction of training and familiarization times: The intuitive user interface allows even workers without specialized programming knowledge to effectively operate and program the robot, reducing costs for training and familiarization times.
User-defined operating view with makro buttons
The custom control view with macro buttons feature allows users to create individual interfaces with personalized macro buttons. This function simplifies interaction with frequently used commands and increases productivity in various applications.
Advantages of user-defined operating view with makro buttons
- Personalization: Customize the interface to suit individual needs and working styles.
- Efficiency: Quicker access to frequently used commands and functions.
- Productivity boost: Time savings and optimized workflows by reducing clicks and menu navigation.
- Flexibility: Easily add, remove, or change macro buttons as needed.
User-defined coordinate systems
The "Custom Coordinate Systems" feature allows for defining and using individual reference frames within a robotic application. These coordinate systems enable precise positioning and alignment of the robot, as well as efficient collaboration with other systems.
Advantages of user-defined coordinate systems
- Orientation: Improves the robot's orientation in complex environments by providing local reference frames for different parts of the workspace.
- Collaboration: Facilitates collaboration between multiple robots or systems by using common coordinate systems.
- Flexibility: Simplifies the integration of new features or adaptations to changing production requirements through the adaptability of coordinate systems.
- Simplification: Makes programming easier by allowing the use of multiple coordinate systems for different tasks or tools.
Access to the Profinet interface
Profinet is a modern, Ethernet-based protocol designed for real-time communication and data exchange between automation components in industrial networks. When robots have the appropriate interface, they can be more efficiently controlled in connection with other automation components and integrated into complex production processes.
Advantages of the profinet interface
-
Fast response time: In a machine loading system, for example, an industrial robot with a Profinet interface can adjust its movements in real-time to the speed of the conveyor belt, ensuring that parts are placed precisely and without delay.
-
Flexibility: Through communication with other machines, a robot can be more easily integrated into an existing production line using the Profinet interface.
-
Scalability: In a dosing application, such as filling liquids into bottles, the Profinet interface allows the networking of multiple robots and machines to ensure uniform and precise dosing across all bottles and increase production capacity.
-
Diagnostics: Remote monitoring of an industrial robot is made possible by the Profinet interface, allowing for faster error correction. For example, when the robot is used for sorting parts, if one of the parts is sorted incorrectly.
-
Energy efficiency: With a Profinet interface, the robot's energy consumption can be optimized by, for example, switching to an energy-saving mode during standby times.
Access to the modbus interface
Modbus is a widely-used, serial communication protocol that enables the connection of industrial electronic devices, such as sensors, actuators, and controllers. In the field of automation, Modbus is used for communication and coordination between robots and other machines.
Advantages of the modbus interface
-
Easy integration: Due to the widespread use of Modbus in the industry, it is easy to integrate an industrial robot with a Modbus interface into existing systems and machines without having to make extensive adjustments.
-
Cost efficiency: Modbus is a cost-effective communication protocol that does not incur expensive hardware or licensing costs, making it attractive for companies with limited budgets.
-
Open protocol: As Modbus is an open protocol, devices from different manufacturers can communicate with each other without issues, which expands the selection of compatible devices and systems.
-
Simple troubleshooting and maintenance: By using Modbus, industrial robots can relay information about their operating status to higher-level control systems. This allows for easier troubleshooting and maintenance, as potential disruptions can be detected and addressed early on.
Primary interface for external function callsThe feature "Access to the primary interface for executing external function calls" enables a robot to access external functions and execute them within its program flow. XML-RPC is used as the primary interface, allowing the robot to function as a "slave" and be controlled by an external device, the "master". |
|
![]() |
|
Benefits of the primary interface:
|
AI Copilot
Benefit from the best context-sensitive real-time support. Program more efficiently through AI optimization of programs and AI-assisted creation of program modules and functions
Your advantages:
- Maximum time & cost efficiency in support: Questions & assistance without support calls - with the AI Copilot you receive context-sensitive answers in real time. So you can continue quickly, even if you encounter problems when creating programmes.
- Your personal trainer: Further training through sparring with the AI Copilot, just like with a trainer, application or service technician.
AI Programming
Support in the creation of complex programmes
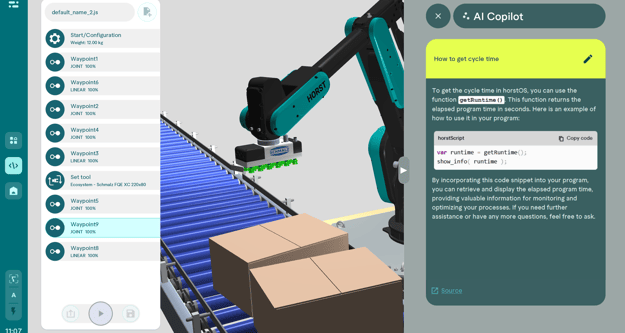
Your advantages of AI Programming
- Most efficient programming: AI generation of functions, programme modules and programme templates
- Optimisation and correction of programs: Syntax analysis and output of optimisation options
AI Error Handling
The AI Copilot goes beyond simple fault detection.
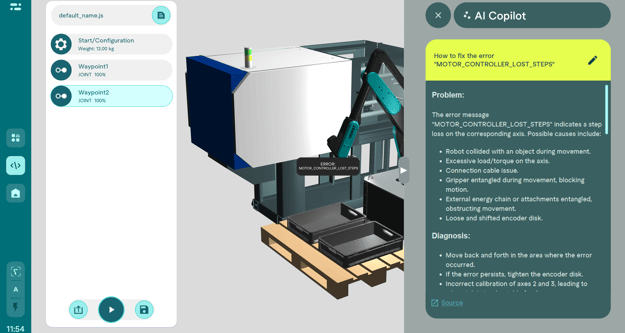
Your advantages of AI Error Handling
- Comprehensive analysis in the event of an error: It analyses your project setup, your program logic and even your hardware configurations to determine the cause of problems. It then provides actionable recommendations and potential solutions, saving you valuable time and frustration.
- Transfer error messages directly to the co-pilot: If an error message occurs, it can be transferred directly to the AI Copilot for analysis.
Component Management
Advantages of centralised component management
- Simple creation of components: Quick step-by-step setup and configuration of connected components
- Single point of control: Direct access to the component interface. Enormous time savings through setup, operation and making adjustments from a central point.
Process Control
Advantages of customised process control
- Simple operation and a good overview: By customising the Process Control, the operator can be provided with exactly the functions they need during operation. This minimises errors caused by incorrect operation
- Flexible set-up: The most important functions (e.g. release door or open gripper) can be made directly accessible in the Process Control.
3. Additional Robot Services
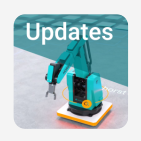
Access to the latest software
Access to the latest software releases enables you to benefit from the continuous further development of the robot software and remain flexible in the event of changing requirements. This leads to greater efficiency and better performance of the robot in various applications
You receive regular updates during the runtime. The updates relate to the complete horstFX + horstOS software. The updates are made available via the IIoT platform horstCOSMOS. You can decide whether you want to carry out the update or not.
Service-Hotline
A service hotline provides prompt and expert assistance for users experiencing technical issues or difficulties with the robot, its operating software, or its applications. This helps minimize potential downtime and keeps operations running smoothly.
If service is required, our robot experts can be reached via a service telephone number on weekdays from 8 am to 5 pm.
Technical advice from qualified robot experts
Experienced robot experts are available to advise you on how to exploit the full potential of your digital robot during operation.
- Systematic troubleshooting and support in the event of problems or errors
- Technical advice and program optimization
- Assistance...
- for queries about setting up the robot system
- for programming with horstFX
- with the optimization of programs and cycle times
- Assistance...
- Remote support: A robot expert from fruitcore robotics connects live to the robot system (permanent or temporary internet connection required)
When prioritizing the existing requests, it is taken into account whether a Care or Care Plus service contract is active for the robot system
Wear warranty
With this warranty, you are covered when it comes to replacing wearing parts such as belts or external cables - including the cost of the spare parts themselves.
The need to replace wearing parts results from permanent system monitoring (permanent internet connection required) or regular system checks. The replacement of wearing parts can be carried out by the customer under instruction and with the prior approval of fruitcore robotics, otherwise by a partner or an employee of fruitcore robotics.
System check if necessary (remote or on-site)
Regular system checks are an integral part of our predictive maintenance approach. By continuously monitoring the condition of our intelligent industrial robots using the IIoT platform, potential problem areas can be identified at an early stage and rectified preventively. If a system check is necessary, this is usually carried out conveniently via a remote connection, which means that your operating processes are interrupted for as little time as possible. If necessary, the inspection is carried out by one of our robot experts on site.
Extended warranty for entire robot system
While the statutory warranty covers claims for defects within the prescribed period, the long-term warranty guarantees additional protection and security in the event of possible defects or malfunctions over its entire service life of the robot.
Advantages of this feature in practice
-
The extended warranty reduces the likelihood of production downtime due to robot failure or damage, resulting in improved and consistent productivity.
-
Maintenance cost calculation and predictability is improved by eliminating unexpected repair or replacement costs within the warranty period.
-
An extended warranty allows the robot system to be kept in optimal condition at all times, which can enable greater operating efficiency and maximum system availability.
Spare parts flat rate and delivery
A spare parts flat rate and delivery is an exclusive additional offer to ensure maximum safety and efficiency. This is how we ensure maximum availability of your robot system.
Spare parts are dispatched within one working day of notification of need. In order to clarify all technical details, spare parts are always dispatched on the next working day after receipt of the notification.
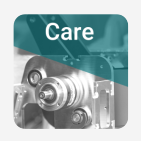
Access to the latest software
Access to the latest software releases enables you to benefit from the continuous further development of the robot software and remain flexible in the event of changing requirements. This leads to greater efficiency and better performance of the robot in various applications
You receive regular updates during the runtime. The updates relate to the complete horstFX + horstOS software. The updates are made available via the IIoT platform horstCOSMOS. You can decide whether you want to carry out the update or not.
Service-Hotline
A service hotline provides prompt and expert assistance for users experiencing technical issues or difficulties with the robot, its operating software, or its applications. This helps minimize potential downtime and keeps operations running smoothly.
If service is required, our robot experts can be reached via a service telephone number on weekdays from 8 am to 5 pm.
Technical advice from qualified robot experts
Experienced robot experts are available to advise you on how to exploit the full potential of your digital robot during operation.
- Systematic troubleshooting and support in the event of problems or errors
- Technical advice and program optimization
- Assistance...
- for queries about setting up the robot system
- for programming with horstFX
- with the optimization of programs and cycle times
- Assistance...
- Remote support: A robot expert from fruitcore robotics connects live to the robot system (permanent or temporary internet connection required)
When prioritizing the existing requests, it is taken into account whether a Care or Care Plus service contract is active for the robot system
Wear warranty
With this warranty, you are covered when it comes to replacing wearing parts such as belts or external cables - including the cost of the spare parts themselves.
The need to replace wearing parts results from permanent system monitoring (permanent internet connection required) or regular system checks. The replacement of wearing parts can be carried out by the customer under instruction and with the prior approval of fruitcore robotics, otherwise by a partner or an employee of fruitcore robotics.
System check if necessary (remote or on-site)
Regular system checks are an integral part of our predictive maintenance approach. By continuously monitoring the condition of our intelligent industrial robots using the IIoT platform, potential problem areas can be identified at an early stage and rectified preventively. If a system check is necessary, this is usually carried out conveniently via a remote connection, which means that your operating processes are interrupted for as little time as possible. If necessary, the inspection is carried out by one of our robot experts on site.
Extended warranty for entire robot system
While the statutory warranty covers claims for defects within the prescribed period, the long-term warranty guarantees additional protection and security in the event of possible defects or malfunctions over its entire service life of the robot.
Advantages of this feature in practice
-
The extended warranty reduces the likelihood of production downtime due to robot failure or damage, resulting in improved and consistent productivity.
-
Maintenance cost calculation and predictability is improved by eliminating unexpected repair or replacement costs within the warranty period.
-
An extended warranty allows the robot system to be kept in optimal condition at all times, which can enable greater operating efficiency and maximum system availability.
Spare parts flat rate and delivery
A spare parts flat rate and delivery is an exclusive additional offer to ensure maximum safety and efficiency. This is how we ensure maximum availability of your robot system.
Spare parts are dispatched within one working day of notification of need. In order to clarify all technical details, spare parts are always dispatched on the next working day after receipt of the notification.
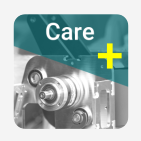
Access to the latest software
Access to the latest software releases enables you to benefit from the continuous further development of the robot software and remain flexible in the event of changing requirements. This leads to greater efficiency and better performance of the robot in various applications
You receive regular updates during the runtime. The updates relate to the complete horstFX + horstOS software. The updates are made available via the IIoT platform horstCOSMOS. You can decide whether you want to carry out the update or not.
Service-Hotline
A service hotline provides prompt and expert assistance for users experiencing technical issues or difficulties with the robot, its operating software, or its applications. This helps minimize potential downtime and keeps operations running smoothly.
If service is required, our robot experts can be reached via a service telephone number on weekdays from 8 am to 5 pm.
Technical advice from qualified robot experts
Experienced robot experts are available to advise you on how to exploit the full potential of your digital robot during operation.
- Systematic troubleshooting and support in the event of problems or errors
- Technical advice and program optimization
- Assistance...
- for queries about setting up the robot system
- for programming with horstFX
- with the optimization of programs and cycle times
- Assistance...
- Remote support: A robot expert from fruitcore robotics connects live to the robot system (permanent or temporary internet connection required)
When prioritizing the existing requests, it is taken into account whether a Care or Care Plus service contract is active for the robot system
Wear warranty
With this warranty, you are covered when it comes to replacing wearing parts such as belts or external cables - including the cost of the spare parts themselves.
The need to replace wearing parts results from permanent system monitoring (permanent internet connection required) or regular system checks. The replacement of wearing parts can be carried out by the customer under instruction and with the prior approval of fruitcore robotics, otherwise by a partner or an employee of fruitcore robotics.
System check if necessary (remote or on-site)
Regular system checks are an integral part of our predictive maintenance approach. By continuously monitoring the condition of our intelligent industrial robots using the IIoT platform, potential problem areas can be identified at an early stage and rectified preventively. If a system check is necessary, this is usually carried out conveniently via a remote connection, which means that your operating processes are interrupted for as little time as possible. If necessary, the inspection is carried out by one of our robot experts on site.
Extended warranty for entire robot system
While the statutory warranty covers claims for defects within the prescribed period, the long-term warranty guarantees additional protection and security in the event of possible defects or malfunctions over its entire service life of the robot.
Advantages of this feature in practice
-
The extended warranty reduces the likelihood of production downtime due to robot failure or damage, resulting in improved and consistent productivity.
-
Maintenance cost calculation and predictability is improved by eliminating unexpected repair or replacement costs within the warranty period.
-
An extended warranty allows the robot system to be kept in optimal condition at all times, which can enable greater operating efficiency and maximum system availability.
Spare parts flat rate and delivery
A spare parts flat rate and delivery is an exclusive additional offer to ensure maximum safety and efficiency. This is how we ensure maximum availability of your robot system.
Spare parts are dispatched within one working day of notification of need. In order to clarify all technical details, spare parts are always dispatched on the next working day after receipt of the notification.
Access to the latest software
Access to the latest software releases enables you to benefit from the continuous further development of the robot software and remain flexible in the event of changing requirements. This leads to greater efficiency and better performance of the robot in various applications
You receive regular updates during the runtime. The updates relate to the complete horstFX + horstOS software. The updates are made available via the IIoT platform horstCOSMOS. You can decide whether you want to carry out the update or not.
Service-Hotline
A service hotline provides prompt and expert assistance for users experiencing technical issues or difficulties with the robot, its operating software, or its applications. This helps minimize potential downtime and keeps operations running smoothly.
If service is required, our robot experts can be reached via a service telephone number on weekdays from 8 am to 5 pm.
Technical advice from qualified robot experts
Experienced robot experts are available to advise you on how to exploit the full potential of your digital robot during operation.
- Systematic troubleshooting and support in the event of problems or errors
- Technical advice and program optimization
- Assistance...
- for queries about setting up the robot system
- for programming with horstFX
- with the optimization of programs and cycle times
- Assistance...
- Remote support: A robot expert from fruitcore robotics connects live to the robot system (permanent or temporary internet connection required)
When prioritizing the existing requests, it is taken into account whether a Care or Care Plus service contract is active for the robot system
Wear warranty
With this warranty, you are covered when it comes to replacing wearing parts such as belts or external cables - including the cost of the spare parts themselves.
The need to replace wearing parts results from permanent system monitoring (permanent internet connection required) or regular system checks. The replacement of wearing parts can be carried out by the customer under instruction and with the prior approval of fruitcore robotics, otherwise by a partner or an employee of fruitcore robotics.
System check if necessary (remote or on-site)
Regular system checks are an integral part of our predictive maintenance approach. By continuously monitoring the condition of our intelligent industrial robots using the IIoT platform, potential problem areas can be identified at an early stage and rectified preventively. If a system check is necessary, this is usually carried out conveniently via a remote connection, which means that your operating processes are interrupted for as little time as possible. If necessary, the inspection is carried out by one of our robot experts on site.
Extended warranty for entire robot system
While the statutory warranty covers claims for defects within the prescribed period, the long-term warranty guarantees additional protection and security in the event of possible defects or malfunctions over its entire service life of the robot.
Advantages of this feature in practice
-
The extended warranty reduces the likelihood of production downtime due to robot failure or damage, resulting in improved and consistent productivity.
-
Maintenance cost calculation and predictability is improved by eliminating unexpected repair or replacement costs within the warranty period.
-
An extended warranty allows the robot system to be kept in optimal condition at all times, which can enable greater operating efficiency and maximum system availability.
Spare parts flat rate and delivery
A spare parts flat rate and delivery is an exclusive additional offer to ensure maximum safety and efficiency. This is how we ensure maximum availability of your robot system.
Spare parts are dispatched within one working day of notification of need. In order to clarify all technical details, spare parts are always dispatched on the next working day after receipt of the notification.
4. Training and simulation
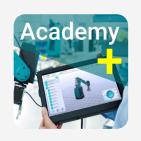
Academy Plus
Our online training platform Academy Plus offers effective and practical training to improve your skills with HORST. Flexible learning, anytime, anywhere.
Academy Plus Training includes the following training content:
• Robot safety
• Setup, commissioning and assembly of the robot system
• Software configuration of the robot via settings
• Manual control of the robot
• Graphical programming with horstFX
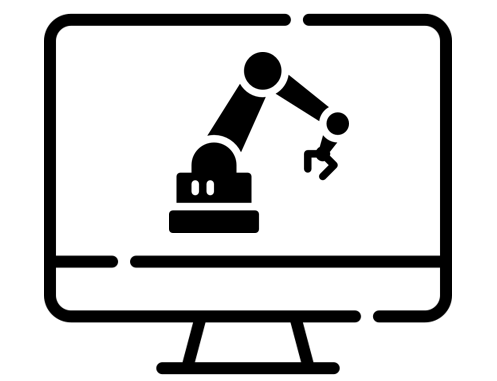
horstFX Simulation
horstFX Simulation enables the effective creation and optimization of robot programs away from the robot as well as the performance of feasibility studies. A horstFX Simulation license entitles you to use horstFX including all additional features on a computer.
• horstFX can be installed on any number of computers
• A license can only be used on one computer at a time
• If a license is retrieved, it is blocked for 24h. After this time it will be released automatically and can be transferred to another computer.
Your selection
Ihre Auswahl
Angebot Anfordern
Information on other products
Mobile Robot Base Station | |
---|---|
Mobile Robot Bases (MRB) | MRB-S, MRB-M, MRB-L (optional with safetyscanner) |
Mobile Robot Base with Safety Fence | MRB-S, MRB-M, MRB-L with safety fence and control panel |
Modular robot base horstCUBE | Expandable robot base with safety technology, control panel and height-adjustable base plate |
End-of-arm | |
---|---|
Double-jaw parallel gripper (electric) | electric 2-finger gripper incl. standard set of gripper jaws, adapter, screws, connection cable and assembly instructions |
Vacuum suction grippers (electric) | electric vacuum unit incl. 2 suction pads, adapter, screws, connection cable and assembly instructions |
Double gripper with blow-off unit (pneumatic) | 2x electric 2-finger gripper with standard set of gripper jaws, blow-off unit, adapter, screws and assembly instructions |
Camera and Safety | |
---|---|
Camera for 2D part recognition | |
Safetyscanner |
Other | |
---|---|
Part-Separation Kit | |
Education Package |
Solution Kits
Pick and Place
The best basic equipment for a safe, flexible, quick and easy introduction to robot-supported automation solutions.
Part Separation
Flexible part separation that is suitable for a wide variety of parts. Efficient, precise and with high repeat accuracy.
Machine Tending
Best cost efficiency and flexibility for machine tending. With this all-round package, you can increase your productivity in the shortest possible time and remain flexible.
Education
The perfect introduction to robotics for educational institutions and apprenticing companies. The package includes teaching material, a training application and desktop licenses for offline programming.
Trainings | |
---|---|
Basic training HORST & horstFX (online or in Constance for max. 3 employees) | |
Additional training for camera interfaces, TCP/IP (online) | |
Additional trainings for SPS interfaces, Profinet (online) | |
Additional trainings textual coding (online) | |
Additional Training Special, individual and project specific | |
Additional Training for Safety (online) | |
Teacher and instructor training (online) |
Are you ready for the automation of the future? Contact us now
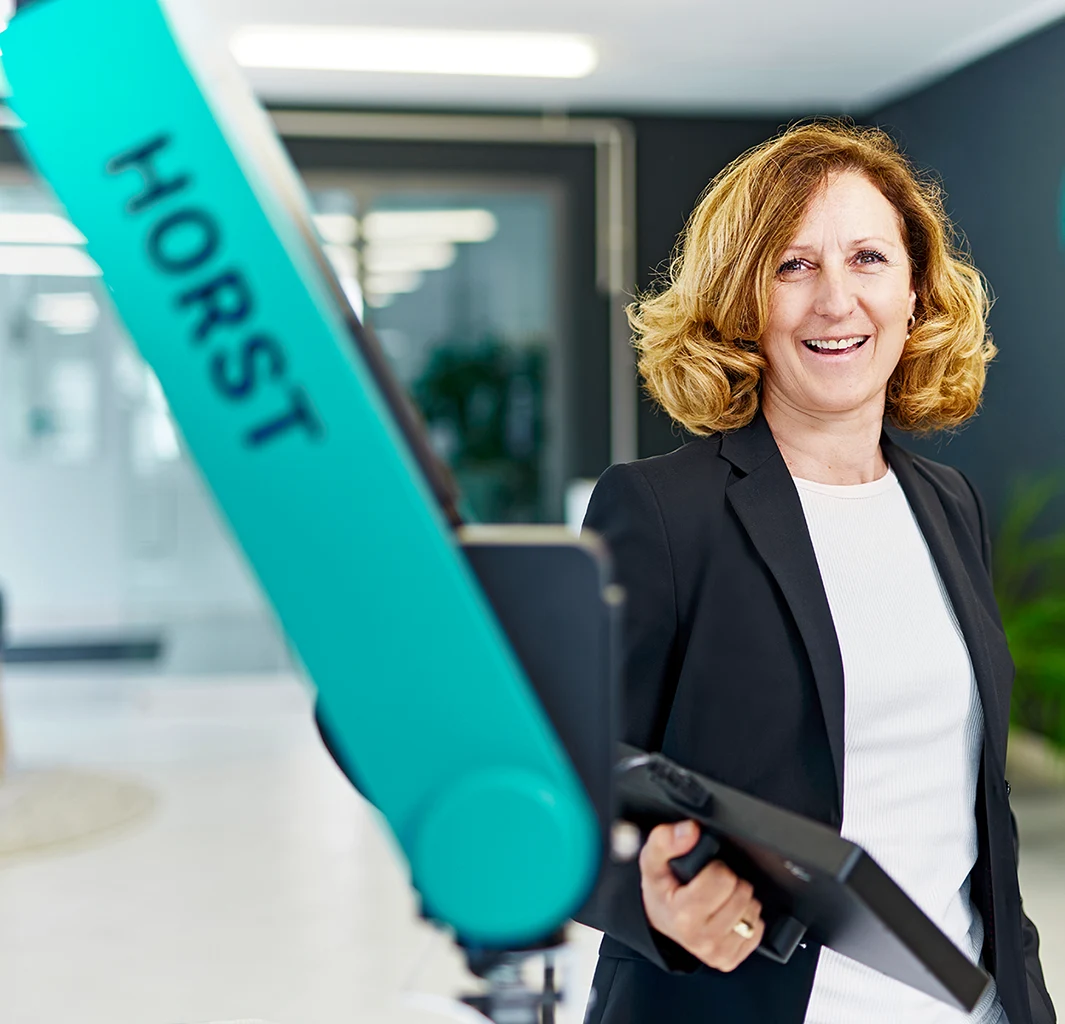